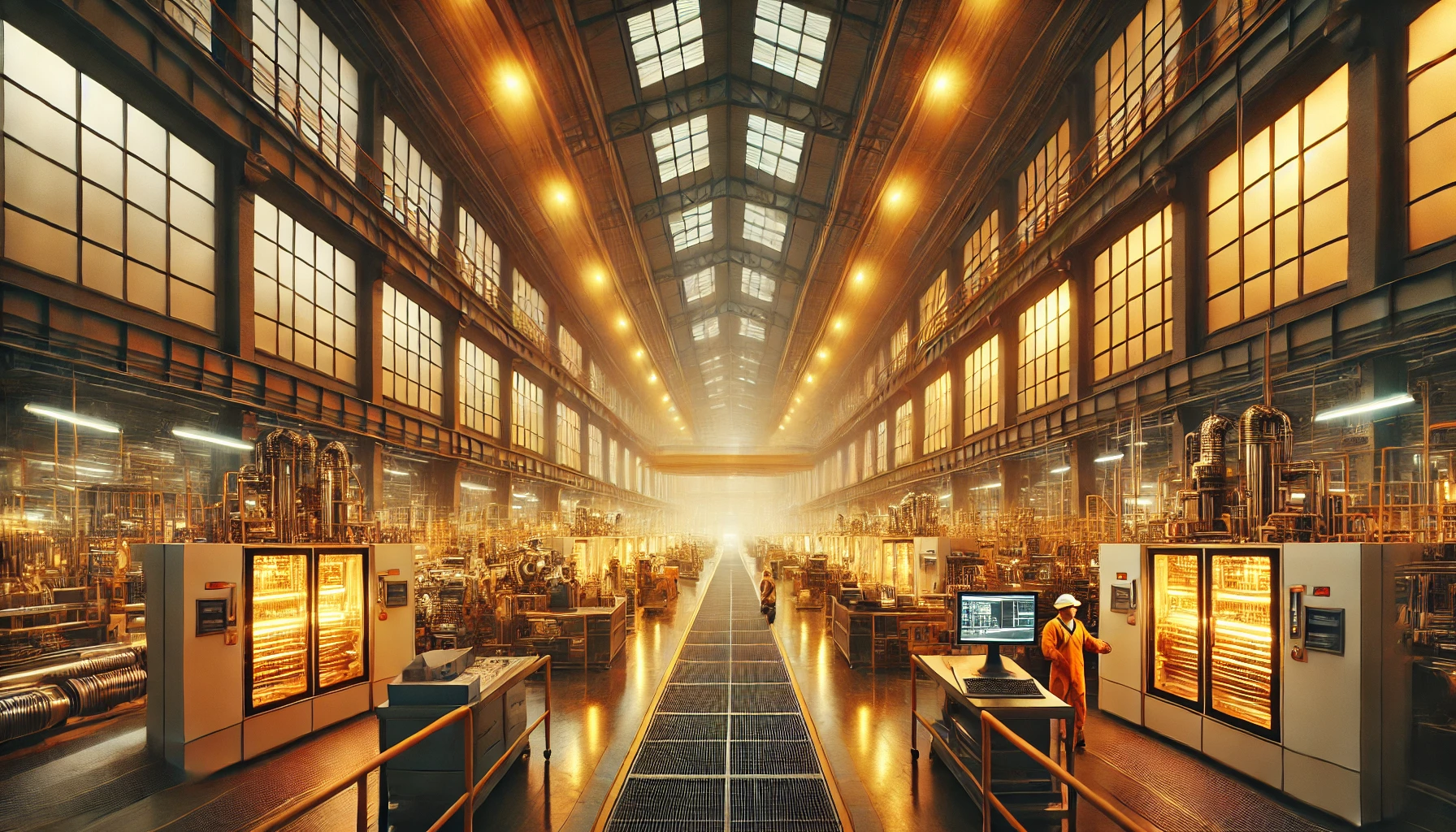
Czy słyszałeś kiedyś sformułowanie „dostosowanie maszyn do wymagań minimalnych„? To częsty termin, który pojawia się, gdy mówimy o starszych maszynach, szczególnie tych, które były użytkowane przed wejściem Polski do Unii Europejskiej. Ale uwaga – to nie to samo co zasadnicze wymagania dla maszyn! Maszyny muszą być zgodne z wymaganiami zasadniczymi, aby mogły być legalnie wprowadzone do obrotu i użytkowane na terenie UE.
Zasadnicze wymagania dla maszyn odnoszą się do przepisów zawartych w Dyrektywie Maszynowej 2006/42/WE oraz nowym Rozporządzeniu ws. Maszyn nr 2023/1230/UE. Oznaczają one wymogi, które muszą zostać spełnione, aby można było przeprowadzić ocenę zgodności, np. nowej linii produkcyjnej, z przepisami Unii Europejskiej. Ale co to dokładnie oznacza? Wyobraź sobie sytuację, w której kupujesz nową linię produkcyjną. Maszyna musi spełniać odpowiednie normy bezpieczeństwa, zanim trafi do Twojego zakładu. Ale co w przypadku starszych maszyn, które zostały zakupione przed wejściem Polski do UE, lub takich sprowadzonych spoza Unii?
Spis Treści
Zasadnicze wymagania dla maszyn: Starsze maszyny i import spoza UE – kiedy trzeba dostosować?
Przykład: W trakcie audytu bezpieczeństwa jednej z firm odkryliśmy interesującą sytuację związaną z maszyną importowaną z Chin. Maszyna ta była oznaczona tzw. „chińskim CE” – oznaczeniem, które dla niewprawionego oka może wyglądać jak znak CE, jednak nie spełniało rzeczywistych standardów UE. Fragment linii, w którym była zamontowana ręczna praska, był chroniony przez kurtynę bezpieczeństwa. Na pierwszy rzut oka wydawało się, że wszystko jest w porządku – przecież była zainstalowana kurtyna! Ale diabeł tkwi w szczegółach.
Po dokładnej analizie okazało się, że system zabezpieczeń był daleki od spełnienia wymagań zasadniczych. Po pierwsze, nie przeprowadzono badań dotyczących dobiegu, czyli reakcji maszyny na nagłe zatrzymanie oraz odległości, jakie muszą być zachowane, aby zapobiec zgnieceniu operatora. Norma EN ISO 13855 wyraźnie określa, jakie minimalne odstępy muszą być zachowane w zależności od czasu reakcji maszyny, co tutaj nie zostało w żaden sposób uwzględnione. Odległość kurtyny bezpieczeństwa była zbyt mała, a czas reakcji za długi, co w praktyce oznaczało, że operator mógłby zostać zgnieciony, zanim maszyna faktycznie by się zatrzymała.
Po drugie, sama kurtyna bezpieczeństwa miała nieodpowiednią rozdzielczość, co oznacza, że nie była w stanie wykryć np. dłoni operatora, co stwarzało realne zagrożenie. Norma EN ISO 13857 dokładnie definiuje wymagania dotyczące szczelin ochronnych oraz minimalnej rozdzielczości zabezpieczeń w zależności od części ciała, które mają być chronione (np. palce, dłonie). W tym przypadku rozdzielczość kurtyny była zbyt mała, aby zapewnić skuteczną ochronę dłoni operatora.
Wynik? Konieczne było nie tylko wymienienie kurtyny na odpowiedni model, ale także przebudowanie całego stanowiska, aby zachować odpowiednie odstępy i dostosować system do wymagań zasadniczych. Takie dostosowanie obejmowało zarówno analizę ryzyka, jak i poprawę całego układu bezpieczeństwa, co oczywiście wiązało się z dodatkowymi kosztami i przestojami produkcyjnymi.
Znak CE nie zawsze gwarantuje bezpieczeństwo
Często zdarza się, że firmy z dumą przedstawiają maszyny z oznakowaniem CE, co teoretycznie potwierdza zgodność z przepisami UE. Niestety, to tylko część prawdy. Znak CE może być nadany na podstawie deklaracji producenta, ale nie zawsze oznacza, że wszystko zostało wykonane zgodnie z normami.
Przykład: W jednej z polskich firm przeprowadziliśmy audyt linii produkcyjnej zbudowanej przez krajowego producenta. Na papierze wszystko wyglądało bez zarzutu – maszyna miała deklarację zgodności WE i nadany znak CE. Jednak po przeprowadzeniu szczegółowej analizy okazało się, że funkcje bezpieczeństwa były zaprojektowane nieprawidłowo, co mogło prowadzić do poważnych zagrożeń.
Jednym z kluczowych problemów było zatrzymanie awaryjne. Zgodnie z normą PN-EN ISO 13850, systemy awaryjnego zatrzymywania muszą zapewnić bezpieczne zatrzymanie maszyny w sytuacji zagrożenia. W przypadku tej linii, po aktywowaniu e-stopu (awaryjnego zatrzymania), siłownik pneumatyczny, który odpowiadał za transport materiału, nie był zabezpieczony odpowiednimi mechanizmami, aby utrzymać ciśnienie w komorze. W praktyce oznaczało to, że materiał mógł opaść po uruchomieniu awaryjnego zatrzymania, co mogło prowadzić do poważnych obrażeń operatorów.
Ten problem wynikał również z błędnej analizy ryzyka. Zgodnie z EN – ISO 12100, w ocenie ryzyka należy uwzględnić wszystkie możliwe źródła zagrożeń, w tym energię potencjalną, która w tym przypadku była zagrożeniem. Opadający materiał transportowany przez siłownik pneumatyczny stwarzał ryzyko zgniecenia operatorów, co było wynikiem niewłaściwego zaprojektowania funkcji bezpieczeństwa. Norma EN – ISO 12100 wyraźnie mówi, że energia potencjalna, zgromadzona w elementach maszyny, musi być kontrolowana, aby zapobiec jej niekontrolowanemu uwolnieniu.
Kolejny problem dotyczył piły. W sytuacji awaryjnego zatrzymania jej bezwładność powodowała, że piła była uszkadzana, a odłamki mogły stanowić zagrożenie dla pracowników. To pokazuje, jak istotne jest uwzględnienie wszystkich aspektów bezwładności i reakcji maszyn w trakcie awaryjnych zatrzymań. Bez odpowiedniego zabezpieczenia, zatrzymanie awaryjne może samo w sobie generować nowe ryzyko, zamiast je eliminować.
Choć formalnie odpowiedzialność za błędy spoczywała na producencie, firma ta niestety splajtowała, co oznaczało, że użytkownik musiał samodzielnie dostosować linię do wymagań zasadniczych. Konieczne było przeprojektowanie funkcji bezpieczeństwa i modyfikacja linii, aby spełniała ona wszystkie odpowiednie normy, co wiązało się z dużymi kosztami i przestojami produkcyjnymi.
W wyniku tego procesu konieczne było:
- Zastosowanie odpowiednich blokad ciśnienia w siłownikach pneumatycznych, co zabezpieczyło materiał przed niekontrolowanym opadaniem.
- Opracowanie systemu, który uwzględniał bezwładność piły, aby zapobiec jej uszkodzeniom podczas zatrzymania awaryjnego, a tym samym zmniejszyć ryzyko wyrzucania odłamków.
Szkolenie
Dyrektywa Maszynowa
2006/42/WE
Zdobądź niezbędną wiedzę o Dyrektywie Maszynowej 2006/42/WE! Zarejestruj się na nasze szkolenie i zapewnij bezpieczeństwo w swoim zakładzie!
Dostosowanie maszyn do wymagań zasadniczych – co to oznacza?
Dostosowanie maszyny do wymagań zasadniczych to nie tylko zmiana kilku elementów. To kompleksowy proces, który może obejmować:
- Odtworzenie lub aktualizację dokumentacji technicznej.
- Ponowne przeprowadzenie obliczeń wytrzymałościowych, aby upewnić się, że maszyna spełnia wymogi bezpieczeństwa.
- Zaprojektowanie nowych funkcji bezpieczeństwa, takich jak systemy zatrzymywania awaryjnego, osłony czy kurtyny bezpieczeństwa.
- Przeprowadzenie analizy ryzyka, która dokładnie określi, jakie zagrożenia mogą wystąpić podczas użytkowania maszyny, i jakie środki należy zastosować, aby je wyeliminować.
Koszty takiego procesu mogą być znaczne, zwłaszcza w przypadku maszyn importowanych spoza UE, które często nie spełniają nawet podstawowych wymagań bezpieczeństwa maszyn. Jednak inwestycja w bezpieczeństwo pracowników i zgodność z przepisami to nie tylko obowiązek prawny, ale także sposób na zapewnienie ciągłości produkcji i uniknięcie potencjalnych wypadków, które mogą prowadzić do poważnych konsekwencji prawnych i finansowych.
Zasadnicze wymagania dla maszyn to nie tylko formalność, którą można zignorować. Każda maszyna, niezależnie od tego, czy jest nowa, czy używana, musi spełniać określone normy bezpieczeństwa, zanim zostanie dopuszczona do użytkowania na terenie Unii Europejskiej. Proces dostosowania maszyn do tych wymagań może być skomplikowany i kosztowny, ale jest niezbędny dla zapewnienia bezpieczeństwa pracowników i uniknięcia poważnych konsekwencji prawnych.
Przypadki, takie jak „chińskie CE” czy linia zbudowana przez polskiego producenta, pokazują, że nie zawsze można polegać na deklaracjach producentów. Audyty, analiza ryzyka i właściwe dostosowanie maszyn do wymagań zasadniczych to kluczowe kroki, które muszą być podjęte, aby chronić zdrowie i życie ludzi, a także zapewnić zgodność z przepisami.
Linki zewnętrzne
https://isap.sejm.gov.pl/isap.nsf/DocDetails.xsp?id=WDU20081991228 – Rozporządzenie Ministra Gospodarki z dnia 21 października 2008 r. w sprawie zasadniczych wymagań dla maszyn
FAQ: Zasadnicze wymagania dla maszyn
Wymagania minimalne odnoszą się do podstawowych standardów bezpieczeństwa dla maszyn już użytkowanych w zakładach pracy. Są one określone w Dyrektywie Narzędziowej 2009/104/WE (wcześniej 89/655/EWG) oraz w polskich przepisach, takich jak Rozporządzenie Ministra Gospodarki w sprawie minimalnych wymagań dotyczących bezpieczeństwa i higieny pracy. Państwowa Inspekcja Pracy (PIP) udostępnia listy kontrolne, które pomagają w ocenie zgodności maszyn z tymi wymaganiami.
Wymagania zasadnicze są określone w Dyrektywie Maszynowej 2006/42/WE oraz Rozporządzeniu UE nr 2023/1230 i dotyczą maszyn wprowadzanych na rynek UE po raz pierwszy. Spełnienie wymagań zasadniczych jest niezbędne do przeprowadzenia oceny zgodności i nadania oznakowania CE.
Jeśli maszyna została zakupiona po wejściu Polski do Unii Europejskiej (1 maja 2004 roku), powinna już spełniać wymagania zasadnicze i posiadać oznakowanie CE. W przypadku maszyn zakupionych przed tym terminem obowiązują głównie wymagania minimalne. Jednakże, jeśli taka maszyna została znacząco zmodyfikowana w sposób wpływający na jej bezpieczeństwo, została sprowadzona spoza UE po 2004 roku, lub jeśli chcesz zapewnić najwyższy poziom bezpieczeństwa w swoim zakładzie, konieczne może być dostosowanie jej do wymagań zasadniczych.
Używanie maszyn, które powinny posiadać oznakowanie CE, ale go nie mają, może prowadzić do poważnych konsekwencji prawnych, finansowych i związanych z bezpieczeństwem. Organy nadzoru mogą nałożyć kary, wstrzymać produkcję, a w przypadku wypadków przy pracy może dojść do odpowiedzialności karnej oraz konieczności wypłaty odszkodowań.
Koszty mogą być znaczne i obejmować:
Odtworzenie dokumentacji technicznej.
Przeprowadzenie obliczeń wytrzymałościowych.
Zaprojektowanie i wdrożenie nowych systemów bezpieczeństwa.
Wykonanie kompleksowej analizy ryzyka.
Wysokość kosztów zależy od stopnia niezbędnych modyfikacji i złożoności maszyny.
Proces obejmuje między innymi następujące etapy:
Ocena aktualnego stanu maszyny i identyfikacja niezgodności z wymaganiami.
Analiza ryzyka zgodnie z normą PN-EN ISO 12100.
Wprowadzenie niezbędnych modyfikacji technicznych.
Sporządzenie kompletnej dokumentacji technicznej.
Przeprowadzenie oceny zgodności i nadanie oznakowania CE.
analiza ryzyka automatyka przemysłowa automatyzacja procesów produkcyjnych automatyzacja produkcji bezpieczeństwo maszyn deklaracja zgodności WE dokumentacja techniczna dostosowanie maszyn do wymagań minimalnych dyrektywa ATEX dyrektywa EMC dyrektywa LVD dyrektywa maszynowa 2006/42/WE GPSD GPSR hazop Instrukcja obsługi integrator automatyki przemysłowej inżynieria procesowa KPI linie produkcyjne maszyna nieukończona mes normy zharmonizowane ocena ryzyka OEE oznakowanie CE Performence level poka-yoke pokrycie diagnostyczne projektowanie maszyn przemysł spożywczy roboty przemysłowe rozporządzenie w sprawie maszyn 2023/1230 sat SCADA SIL smed stanowiska zrobotyzowane TPM zarządzanie zarządzanie projektami Znak CE
Zobacz także:
Napisz do nas!
Chętnie odpowiemy na Twoje pytania!