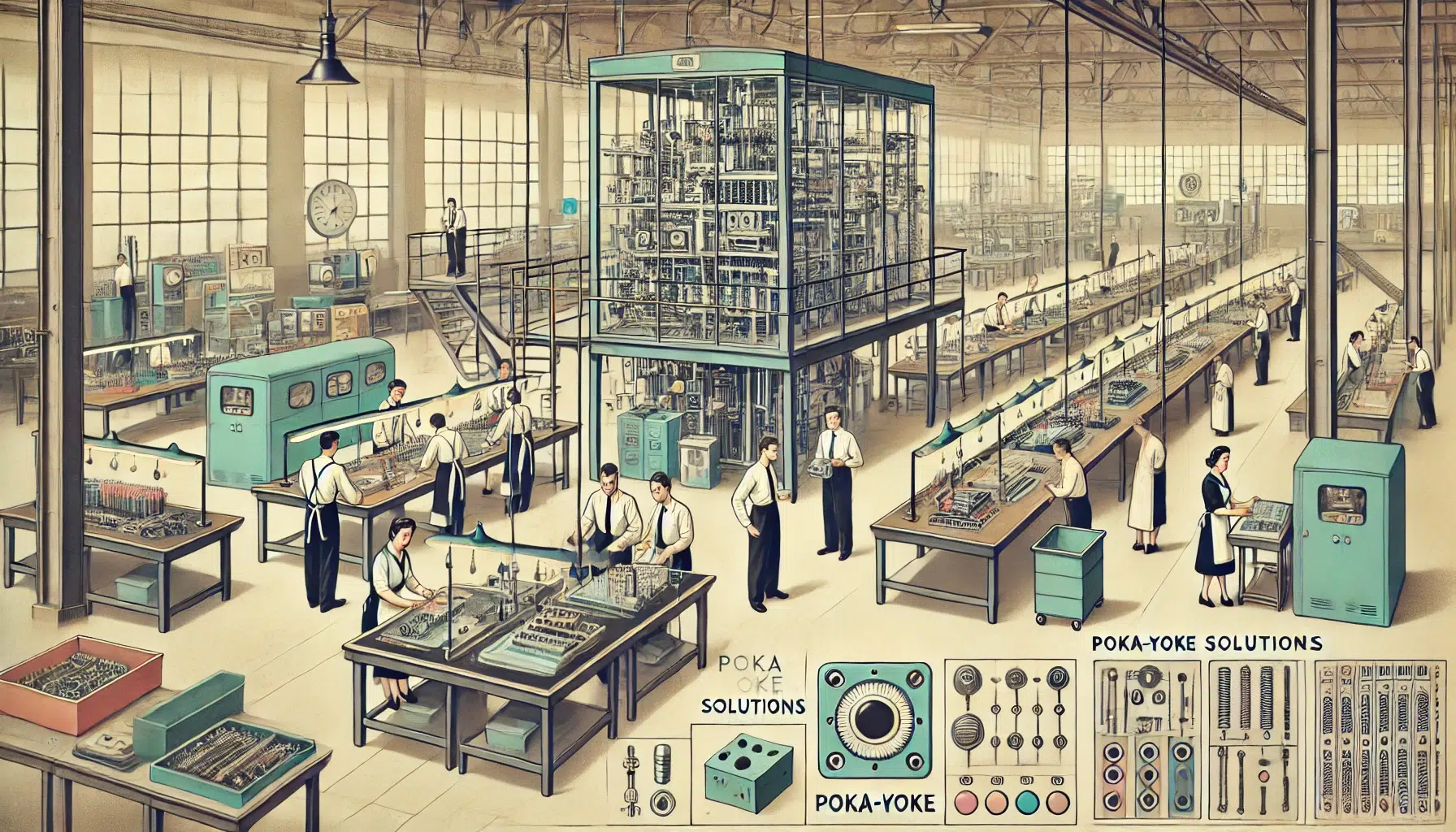
Poka-Yoke to japońska technika zapobiegania błędom, wprowadzona przez Shigeo Shingo w latach 60. XX wieku jako część Systemu Produkcyjnego Toyoty. Jej celem jest projektowanie procesów, w których błędy są fizycznie niemożliwe do popełnienia lub są łatwe do wykrycia i naprawienia, zanim wpłyną na produkt końcowy lub bezpieczeństwo pracowników. W przemyśle, gdzie dąży się do optymalizacji wydajności, minimalizacji odpadów oraz poprawy jakości produktów, Poka-Yoke stało się nieodłącznym elementem strategii produkcyjnych, zwłaszcza w ramach koncepcji lean manufacturing. W niniejszym artykule skupimy się na różnych zastosowaniach Poka-Yoke w trzech kluczowych obszarach: bezpieczeństwie, procesach montażowych oraz poprawności procesu produkcyjnego.
Spis Treści
Bezpieczeństwo na liniach produkcyjnych
Zastosowanie Poka-Yoke w obszarze bezpieczeństwa odgrywa istotną rolę w ochronie pracowników przed wypadkami, zwłaszcza tam, gdzie operatorzy mają do czynienia z ciężkimi maszynami lub robotami przemysłowymi. W takich środowiskach, nawet niewielkie błędy mogą prowadzić do poważnych obrażeń lub uszkodzeń sprzętu. Przykładem rozwiązania z obszaru Poka-Yoke są maty bezpieczeństwa, które rozmieszczone wokół niebezpiecznych maszyn automatycznie zatrzymują urządzenie, gdy operator nieumyślnie wejdzie na strefę zagrożenia. Dzięki temu wypadki są natychmiastowo unikanie, co minimalizuje ryzyko obrażeń.
Kolejnym ważnym rozwiązaniem są czujniki pozycji osłon maszyn. Tego rodzaju systemy blokują uruchomienie urządzeń, gdy ich osłony są podniesione lub zdjęte, zapobiegając przypadkowemu narażeniu operatora na kontakt z niebezpiecznymi częściami maszyn. Takie zabezpieczenia są powszechnie stosowane w przemyśle ciężkim i motoryzacyjnym, gdzie maszyny często operują na dużych prędkościach i z dużymi siłami. Wspomniane technologie ograniczają liczbę wypadków na liniach produkcyjnych.
Zastosowanie Poka-Yoke obejmuje również automatyczne wyłączniki na liniach robotów przemysłowych, które zatrzymują robota, gdy system wykryje zbliżenie człowieka do strefy pracy maszyny. Współczesne linie produkcyjne coraz częściej bazują na współpracy robotów z ludźmi, co niesie za sobą ryzyko wypadków, jeśli operator wejdzie w obszar działania maszyny. Dzięki takim zabezpieczeniom ryzyko to jest minimalizowane
Poka-Yoke w procesach montażowych
W montażu elementów produkcyjnych stosowanie Poka-Yoke ma na celu wyeliminowanie błędów, które mogą prowadzić do poważnych wad w produktach końcowych. W branży motoryzacyjnej, elektronicznej i innych, gdzie precyzja montażu ma kluczowe znaczenie, najmniejsze odstępstwa od standardu mogą skutkować poważnymi wadami i awariami produktów. Jednym z najczęściej stosowanych rozwiązań w tej dziedzinie są złącza o specjalnym kształcie, które mogą być zamontowane tylko w jednej orientacji. Przykładem mogą być złącza elektroniczne w komputerach lub samochodach, gdzie odpowiednie zaprojektowanie złącz minimalizuje ryzyko błędów montażowych.
Kolejną popularną metodą Poka-Yoke w procesach montażowych są czujniki obecności komponentów, które monitorują, czy wszystkie elementy montażu zostały zamontowane przed przejściem do kolejnej operacji. Przykładem może być liczba śrub montowanych w silniku samochodowym – jeśli brakuje jednej śruby, czujniki natychmiast zatrzymują linię montażową, uniemożliwiając dalszy montaż produktu bez wszystkich komponentów.
Dla poprawy identyfikacji komponentów, zwłaszcza w złożonych procesach montażowych, stosuje się również kolorowe oznaczenia. Dzięki oznaczeniom kolorystycznym operatorzy mogą łatwo i szybko zidentyfikować właściwe komponenty, co zapobiega błędom. Przykłady zastosowania tej techniki można znaleźć w przemyśle motoryzacyjnym, gdzie różne kolory części pomagają w uniknięciu montażu niewłaściwego elementu w nieodpowiednim miejscu.
Poprawność procesu produkcyjnego
Poka-Yoke w obszarze poprawności procesu koncentruje się na eliminowaniu błędów operacyjnych, które mogą prowadzić do wad produktów, niezgodności z normami jakościowymi oraz przestojów produkcyjnych. W nowoczesnych zakładach produkcyjnych procesy te muszą być precyzyjnie kontrolowane, a Poka-Yoke pomaga w wykrywaniu błędów na wczesnym etapie, zanim produkt przejdzie do dalszych etapów produkcji.
Jednym z najczęściej stosowanych rozwiązań w zakresie poprawności procesu są czujniki położenia komponentów. Tego rodzaju czujniki kontrolują, czy każdy komponent jest prawidłowo zamontowany i znajduje się na właściwym miejscu. Przykładem może być linia produkcyjna w branży motoryzacyjnej, gdzie czujniki monitorują liczbę i położenie montowanych śrub. Jeśli jakikolwiek komponent nie jest zamontowany prawidłowo lub brakuje jednego z elementów, proces produkcji zostaje natychmiast zatrzymany, co zapobiega wadom w końcowym produkcie.
W przemyśle spożywczym i farmaceutycznym szeroko stosowane są detektory metalu, które wykrywają zanieczyszczenia metalowe w produktach. Dzięki temu możliwe jest usunięcie z linii produkcyjnej wadliwego produktu przed jego dalszą obróbką lub pakowaniem, co gwarantuje bezpieczeństwo konsumentów. Detektory metalu odgrywają kluczową rolę w minimalizowaniu ryzyka związanego z zanieczyszczeniami, które mogą być niebezpieczne dla zdrowia.
W wielu branżach stosuje się również skalowanie surowców – systemy wagowe, które kontrolują ilość surowców używanych na poszczególnych etapach produkcji. Dzięki temu producent może mieć pewność, że składniki są używane zgodnie z przepisami i specyfikacjami, co zapobiega nadmiernemu lub niewystarczającemu dozowaniu. Tego rodzaju rozwiązania są powszechnie stosowane w przemyśle spożywczym, chemicznym oraz farmaceutycznym.
Kolejnym przykładem Poka-Yoke w procesach produkcyjnych są systemy blokad mechanicznych, które uniemożliwiają rozpoczęcie kolejnego etapu produkcji, dopóki poprzedni nie zostanie zakończony zgodnie z określonymi normami. Jest to szczególnie istotne w produkcji wieloetapowej, gdzie każdy krok musi być precyzyjnie kontrolowany. Blokady te zapewniają, że każdy etap procesu jest zakończony w odpowiedniej kolejności, co minimalizuje błędy i przestoje.
Systemy wizyjne w kontekście Poka-Yoke
Systemy wizyjne stają się coraz bardziej popularnym narzędziem Poka-Yoke w nowoczesnych liniach produkcyjnych, szczególnie tam, gdzie wymagana jest precyzyjna kontrola jakości i eliminacja błędów na dużą skalę. Współczesne technologie umożliwiają stosowanie kamer oraz zaawansowanych algorytmów analizy obrazu, które są w stanie automatycznie wykrywać nieprawidłowości w produktach, monitorować procesy montażowe oraz kontrolować poprawność położenia komponentów.
Systemy wizyjne doskonale sprawdzają się w zastosowaniach takich jak:
- Kontrola jakości w czasie rzeczywistym – Kamery mogą natychmiast analizować, czy produkt spełnia wszystkie wymogi jakościowe, np. czy każdy element jest odpowiednio zamontowany lub czy na powierzchni nie ma wad fabrycznych. Na przykład, w produkcji elektroniki, systemy wizyjne mogą wykrywać nieprawidłowe lutowanie lub uszkodzenia komponentów.
- Weryfikacja poprawności montażu – Systemy wizyjne mogą być używane do monitorowania prawidłowego umieszczenia komponentów na linii montażowej. Przykład: kamera zintegrowana z algorytmem rozpoznawania obrazów jest w stanie wykryć brak lub niewłaściwe położenie śrub na montowanym produkcie, co pozwala na natychmiastowe zatrzymanie linii produkcyjnej w przypadku wykrycia niezgodności.
- Rozpoznawanie barw i kształtów – W zastosowaniach wymagających identyfikacji specyficznych elementów systemy wizyjne potrafią rozróżniać komponenty na podstawie ich koloru lub kształtu, co minimalizuje ryzyko pomyłek. Przykład: w przemyśle spożywczym, kamery monitorują pakowanie produktów, aby upewnić się, że opakowanie zawiera wszystkie wymagane składniki.
Systemy wizyjne są nieocenionym narzędziem wspierającym Poka-Yoke w zapewnieniu zgodności produktów z wymaganiami jakościowymi, a ich zastosowanie stale rośnie w produkcji na szeroką skalę. Zaletą tych systemów jest ich zdolność do pracy w czasie rzeczywistym, co pozwala na natychmiastową reakcję w przypadku wykrycia problemów, co z kolei zapobiega produkcji wadliwych wyrobów.
Zasady Poka-Yoke w projektowaniu maszyn przemysłowych
Uwzględnienie zasad Poka-Yoke już na etapie projektowania maszyn przemysłowych ma kluczowe znaczenie dla późniejszej automatyzacji i łatwego zarządzania procesem produkcyjnym. Dzięki temu można od samego początku eliminować błędy, co przekłada się na większą efektywność, bezpieczeństwo oraz jakość produkcji. Automatyka przemysłowa oparta na Poka-Yoke ułatwia także procesk Certyfikacja maszyn CE.
Współpraca z biurem konstrukcyjnym i integratorami automatyki przemysłowej umożliwia lepsze dostosowanie maszyn do procesów produkcyjnych. Dzięki temu, automatyzacja procesów produkcyjnych i automatyzacja produkcji stają się bardziej wydajne i bezpieczne, co pozytywnie wpływa na cały proces budowy maszyn przemysłowych oraz bezpieczeństwo maszyn na liniach produkcyjnym.
Przykłady zastosowania Poka-Yoke w przemyśle produkcyjnym
Poniżej przedstawiamy kilka przykładów zastosowań Poka-Yoke w różnych branżach produkcyjnych, które skutecznie eliminują błędy i poprawiają wydajność procesów.
- Złącza o specjalnym kształcie – W montażu elektroniki, np. w przemyśle komputerowym, złącza o określonych kształtach mogą być zamontowane tylko w jednej, poprawnej orientacji, co eliminuje błędy montażowe.
- Czujniki liczby śrub – W montażu silników samochodowych stosuje się czujniki, które liczą liczbę zamontowanych śrub. Jeśli brakuje choćby jednej, proces montażu zostaje zatrzymany.
- Systemy kolorowe – W przemyśle motoryzacyjnym oraz elektronicznym stosuje się kolorowe oznaczenia na komponentach, aby operatorzy mogli łatwo rozróżnić elementy i uniknąć błędów montażowych.
- Detektory metalu – W przemyśle spożywczym i farmaceutycznym detektory metalu wykrywają zanieczyszczenia metalowe, które mogą trafić do produktów w wyniku procesów produkcyjnych.
- Skalowanie surowców – Systemy wagowe w przemyśle chemicznym i spożywczym zapewniają odpowiednią ilość składników, co eliminuje błędy związane z niewłaściwym dozowaniem.
- Interlock switches – W fabrykach, gdzie bezpieczeństwo jest priorytetem, interlock switches blokują uruchomienie maszyn, jeśli osłony ochronne nie są na swoim miejscu.
- Światła sygnalizacyjne – Światła na liniach montażowych informują operatorów o stanie procesu, dzięki czemu mogą oni szybko reagować na pojawiające się błędy lub awarie.
- Maty bezpieczeństwa – Rozmieszczone wokół niebezpiecznych maszyn maty automatycznie zatrzymują produkcję, gdy ktoś wejdzie na matę, zapobiegając wypadkom.
- Systemy kodów kreskowych – W fabrykach stosuje się systemy skanowania kodów kreskowych, aby upewnić się, że odpowiednie komponenty są używane we właściwych miejscach.
- Czujniki obrotów – Na liniach zrobotyzowanych czujniki obrotów wykrywają niewłaściwe ruchy robotów i zatrzymują proces, aby uniknąć uszkodzeń komponentów.