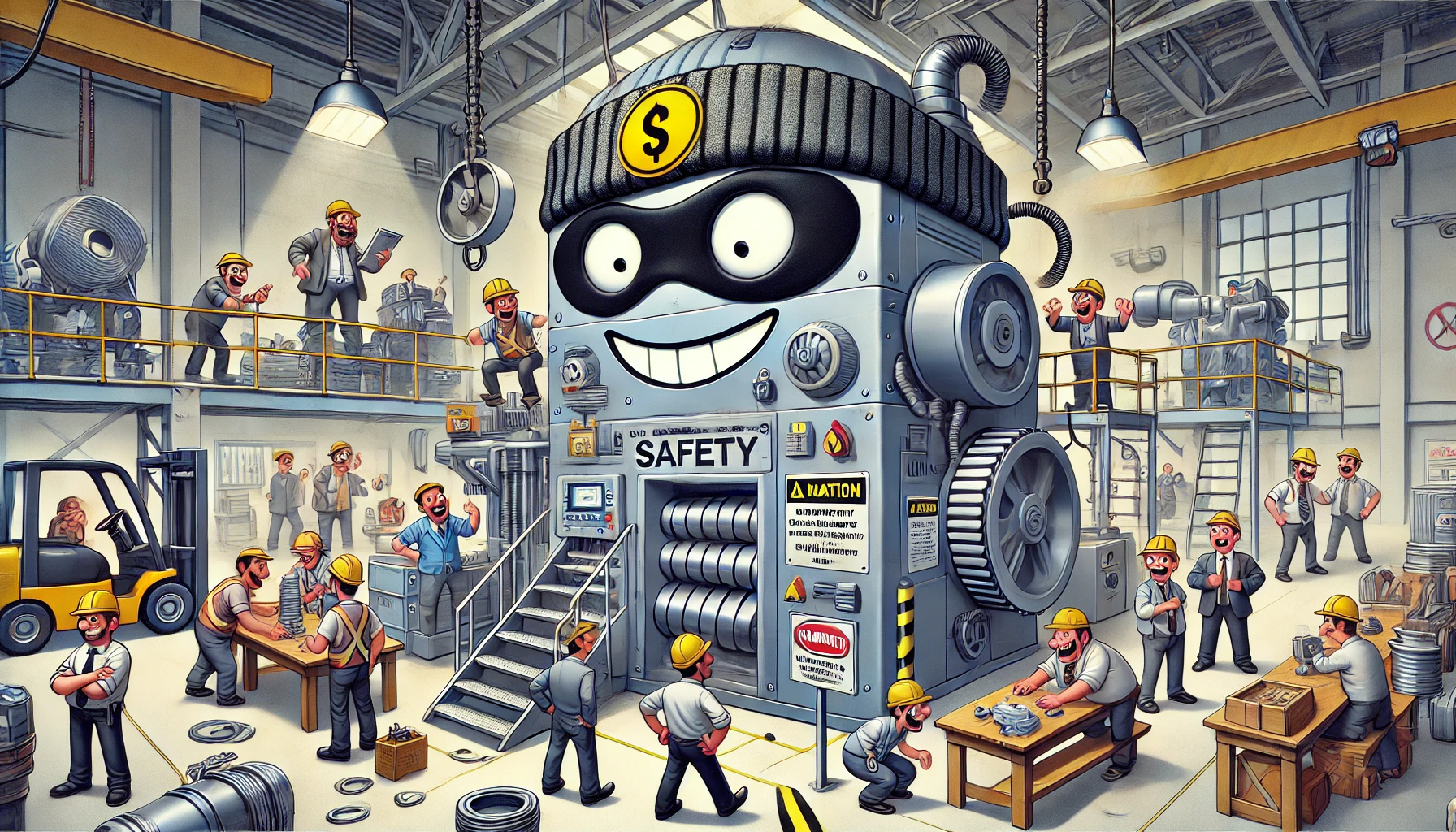
Bezpieczeństwo maszyn jest jednym z najważniejszych aspektów w nowoczesnym przemyśle. Bez odpowiednich środków ochronnych, zarówno pracownicy, jak i produkcja są narażeni na ryzyko awarii i wypadków. W tym artykule omówimy kluczowe aspekty bezpieczeństwa maszyn, najlepsze praktyki oraz regulacje, które pomagają zapewnić bezpieczne środowisko pracy.
Spis Treści
Bezpieczeństwo maszyn: podstawy
Bezpieczeństwo maszyn odnosi się do zestawu środków i praktyk mających na celu zapobieganie wypadkom i minimalizację ryzyka związanego z użytkowaniem maszyn. Dyrektywa Maszynowa 2006/42/WE stanowi podstawę prawną dla bezpieczeństwa maszyn w Unii Europejskiej, określając wymagania dotyczące projektowania, produkcji i użytkowania maszyn.
Automatyka przemysłowa ma ogromny wpływ na bezpieczeństwo maszyn. Z jednej strony automatyzacja zwiększa wydajność, ale z drugiej może wprowadzać nowe zagrożenia. Przykładowo, automatyczne linie produkcyjne mogą prowadzić do poważnych wypadków, jeśli nie są odpowiednio zabezpieczone. Dlatego też audyt bezpieczeństwa jest niezbędny, aby zidentyfikować potencjalne ryzyka i wdrożyć środki zapobiegawcze.
Audyt i analiza ryzyka
Audyt bezpieczeństwa jest kluczowym elementem w ocenie ryzyka związanego z maszynami. Firmy takie jak nasza specjalizują się w przeprowadzaniu audytów, które pomagają zidentyfikować potencjalne zagrożenia i wdrożyć odpowiednie środki zapobiegawcze. Ocena ryzyka wg PN-EN ISO 12100 jest powszechnie stosowaną metodą identyfikacji i oceny ryzyka na różnych etapach życia maszyny.
Biura konstrukcyjne już na etapie projektowania maszyn i linii produkcyjnych dbają o to, aby były one bezpieczne. Oznacza to nie tylko stosowanie odpowiednich norm, ale także dokładne obliczenia wytrzymałościowe (MES) oraz inne analizy numeryczne, które pomagają tworzyć bezpieczne konstrukcje. Dzięki temu możliwe jest zapobieganie awariom i wypadkom na etapie produkcji.
Bezpieczeństwo maszyn: Certyfikacja CE i dostosowanie maszyn
Procedura oceny zgodności
Proces certyfikacji CE maszyn (nazwa nieformalna, prawidłowo proces oceny zgodności maszyn) jest niezbędny, aby maszyny mogły być legalnie wprowadzone na rynek Unii Europejskiej. Jest to formalna procedura oceny zgodności z Dyrektywą Maszynową 2006/42/WE oraz nadania znaku CE. Procedura oceny zgodności składa się z kilku etapów:
- Identyfikacja odpowiednich wymagań: Na początku należy zidentyfikować, które dyrektywy i normy zharmonizowane mają zastosowanie do danej maszyny.
- Ocena ryzyka: Producent musi przeprowadzić ocenę ryzyka zgodnie z normą PN-EN ISO 12100:2012. Proces ten obejmuje identyfikację potencjalnych zagrożeń, ocenę ryzyka i określenie odpowiednich środków zapobiegawczych.
- Dokumentacja techniczna: Producent musi sporządzić szczegółową dokumentację techniczną, która zawiera m.in. rysunki techniczne, schematy elektryczne, obliczenia wytrzymałościowe, raporty z badań, instrukcje obsługi oraz deklarację zgodności.
- Deklaracja zgodności i znak CE: Po spełnieniu wszystkich wymagań, producent sporządza deklarację zgodności WE, w której potwierdza, że maszyna spełnia wszystkie stosowne wymagania. Następnie maszyna zostaje oznakowana znakiem CE.
- Przechowywanie dokumentacji: Producent jest zobowiązany do przechowywania dokumentacji technicznej przez co najmniej 10 lat od daty wyprodukowania ostatniego egzemplarza maszyny.
Ocena ryzyka
Ocena ryzyka jest kluczowym elementem w zapewnieniu bezpieczeństwa maszyn. Proces ten obejmuje następujące etapy:
- Identyfikacja zagrożeń: Na tym etapie identyfikuje się wszystkie potencjalne zagrożenia związane z użytkowaniem maszyny, takie jak zagrożenia mechaniczne, elektryczne, termiczne, chemiczne i inne.
- Ocena ryzyka: Następnie ocenia się prawdopodobieństwo wystąpienia danego zagrożenia oraz jego potencjalne skutki. Ryzyko jest klasyfikowane na podstawie tych dwóch czynników.
- Środki zapobiegawcze: Na podstawie oceny ryzyka określa się odpowiednie środki zapobiegawcze, które mają na celu eliminację lub minimalizację ryzyka. Mogą to być środki techniczne, organizacyjne lub proceduralne.
- Weryfikacja: Po wdrożeniu środków zapobiegawczych, przeprowadza się weryfikację, aby upewnić się, że ryzyko zostało skutecznie zredukowane. W razie potrzeby, proces oceny ryzyka jest powtarzany, aż do osiągnięcia akceptowalnego poziomu bezpieczeństwa.
Kategoria Wymagania | Opis | Przykłady Środków Realizacji |
---|---|---|
Bezpieczeństwo konstrukcji | Maszyny muszą być projektowane tak, aby minimalizować ryzyko | Osłony, systemy blokady, awaryjne wyłączniki |
Dokumentacja techniczna | Szczegółowa dokumentacja musi być dostępna | Rysunki techniczne, schematy, instrukcje obsługi |
Ocena ryzyka | Producent musi przeprowadzić ocenę ryzyka | Analiza zagrożeń, obliczenia wytrzymałościowe |
Bezpieczeństwo maszyn: Dostosowanie maszyn i wymagania minimalne
Dyrektywa narzędziowa
Dostosowanie starszych maszyn do wymagań minimalnych jest kluczowe, aby zapewnić ich zgodność z aktualnymi normami bezpieczeństwa. Niektóre maszyny, które były w użytku przed wprowadzeniem Dyrektywy Maszynowej 2006/42/WE, mogą wymagać dodatkowych działań w celu dostosowania ich do obecnych standardów. Dostosowanie maszyn do wymagań minimalnych obejmuje:
- Przegląd i ocena stanu technicznego: Przeprowadzenie dokładnej analizy technicznej maszyny w celu oceny jej aktualnego stanu i identyfikacji obszarów, które wymagają modernizacji.
- Modernizacja fizyczna: Wprowadzenie niezbędnych zmian i modernizacji w konstrukcji maszyny, takich jak montaż osłon, systemów bezpieczeństwa, blokad i innych urządzeń ochronnych.
- Aktualizacja dokumentacji: Sporządzenie lub aktualizacja dokumentacji technicznej maszyny, w tym instrukcji obsługi, schematów elektrycznych i mechanicznych, oraz dokumentacji dotyczącej oceny ryzyka.
- Szkolenie personelu: Zapewnienie odpowiedniego przeszkolenia dla operatorów i personelu obsługującego maszynę w zakresie nowych procedur i środków bezpieczeństwa.
Dyrektywa narzędziowa 2009/104/WE
Dyrektywa narzędziowa 2009/104/WE, znana również jako dyrektywa dotycząca użytkowania narzędzi pracy przez pracowników, określa minimalne wymagania dotyczące bezpieczeństwa użytkowania narzędzi pracy. Dyrektywa ta ma na celu zapewnienie, że narzędzia pracy, w tym maszyny, są używane w sposób bezpieczny i zgodny z przeznaczeniem. Wymagania minimalne obejmują:
- Bezpieczeństwo konstrukcji: Narzędzia pracy muszą być projektowane i konstruowane w sposób zapewniający ich bezpieczne użytkowanie. Dotyczy to zarówno nowych, jak i używanych narzędzi.
- Instrukcje i szkolenia: Pracodawcy są zobowiązani do dostarczania pracownikom jasnych instrukcji obsługi oraz zapewnienia odpowiedniego szkolenia w zakresie bezpiecznego użytkowania narzędzi pracy.
- Regularne przeglądy i konserwacja: Narzędzia pracy muszą być regularnie przeglądane, konserwowane i testowane, aby zapewnić ich sprawność i bezpieczeństwo.
- Środki ochrony indywidualnej: Pracodawcy muszą zapewnić pracownikom odpowiednie środki ochrony indywidualnej (ŚOI), takie jak kaski, rękawice, okulary ochronne, w sytuacjach, gdy jest to wymagane.
- Ergonomia: Narzędzia pracy powinny być zaprojektowane z uwzględnieniem zasad ergonomii, aby minimalizować ryzyko urazów związanych z niewłaściwym użytkowaniem lub nadmiernym obciążeniem fizycznym pracowników.
Implementacja wymagań wynikających z dyrektywy narzędziowej oraz odpowiednie dostosowanie maszyn i narzędzi pracy do aktualnych standardów są kluczowe dla zapewnienia bezpiecznego środowiska pracy. Przestrzeganie tych regulacji pomaga minimalizować ryzyko wypadków i chronić zdrowie pracowników, co jest fundamentalnym elementem skutecznego zarządzania bezpieczeństwem w przemyśle.
Bezpieczeństwo maszyn: Projektowanie i zarządzanie projektami
Projektowanie maszyn z naciskiem na bezpieczeństwo jest fundamentem tworzenia bezpiecznego środowiska pracy. Biura konstrukcyjne już na etapie koncepcji dbają o to, aby maszyny i linie produkcyjne były bezpieczne, m.in. poprzez ocenę ryzyka wg PN EN ISO 12100. Zarządzanie projektami odgrywa kluczową rolę w tworzeniu nowych rozwiązań. Klient ma ustalony budżet, a rozwiązania muszą być bezpieczne. Współpraca klient-dostawca jest niezbędna, aby znaleźć kompromis między marzeniami a realnymi możliwościami.
Podczas projektowania maszyn, inżynierowie muszą brać pod uwagę nie tylko wydajność, ale także bezpieczeństwo użytkowników. Oznacza to stosowanie odpowiednich norm, takich jak normy zharmonizowane, oraz uwzględnianie wyników analiz ryzyka wg PN-EN ISO 12100:2012. Dzięki temu można zidentyfikować i zarządzać ryzykiem na etapie projektowania, co znacznie zwiększa bezpieczeństwo końcowego produktu.
Automatyka przemysłowa i nowe technologie
Automatyka przemysłowa znacząco wpływa na bezpieczeństwo maszyn. Chociaż automatyzacja może zwiększać wydajność, niesie też ze sobą potencjalne zagrożenia. Przemysł 4.0 wprowadza nowe technologie, które mogą poprawić bezpieczeństwo maszyn, ale wymagają też nowego podejścia do zarządzania ryzykiem.
Programowanie PLC (Programmable Logic Controller) jest kluczowym elementem w automatyzacji procesów przemysłowych. Dzięki odpowiedniemu programowaniu możliwe jest stworzenie bezpiecznych i niezawodnych systemów sterowania, które minimalizują ryzyko awarii i wypadków. Integratorzy automatyki przemysłowej odgrywają tutaj kluczową rolę, zapewniając, że wszystkie elementy systemu współpracują ze sobą w sposób bezpieczny i efektywny.
Wsparcie i outsourcing inżynierów
Outsourcing inżynierów jest skutecznym sposobem na zapewnienie wysokiego poziomu bezpieczeństwa już na etapie koncepcji nowych maszyn i linii produkcyjnych. Współpraca z biurem konstrukcyjnym i integratorami automatyki przemysłowej może znacząco poprawić bezpieczeństwo i efektywność procesów produkcyjnych.
Dzięki outsourcingowi inżynierów, firmy mogą korzystać z wiedzy i doświadczenia specjalistów, którzy pomogą w tworzeniu bezpiecznych maszyn i linii produkcyjnych. Jest to szczególnie ważne w kontekście nowych technologii i automatyzacji procesów produkcyjnych, gdzie wymagane są zaawansowane umiejętności i wiedza.
Zarządzanie projektami i koszty bezpieczeństwa
Zarządzanie projektami to kluczowy element w procesie tworzenia nowych maszyn i linii produkcyjnych. Warto pamiętać, że bezpieczeństwo kosztuje, ale nie można pozwolić sobie na oszczędności kosztem zdrowia i życia pracowników. Dlatego ważne jest, aby ryzyka były identyfikowane i zarządzane na każdym etapie projektu. Współpraca między klientem a dostawcą jest niezbędna, aby znaleźć kompromisy między wymogami bezpieczeństwa a budżetem.
Normy zharmonizowane i przepisy prawne
Normy zharmonizowane odgrywają kluczową rolę w zapewnieniu bezpieczeństwa maszyn. Przestrzeganie tych norm jest niezbędne do uzyskania znaku CE i certyfikacji CE maszyn. Dyrektywa Maszynowa 2006/42/WE oraz inne przepisy prawne określają minimalne wymagania, które muszą być spełnione, aby maszyny mogły być wprowadzone na rynek UE.
Przemysł 4.0 i przyszłość bezpieczeństwa maszyn
Przemysł 4.0 wprowadza nowe technologie, takie jak Internet Rzeczy (IoT), sztuczna inteligencja (AI) oraz robotyka, które mogą znacznie poprawić bezpieczeństwo maszyn. Nowoczesne systemy monitorowania i diagnostyki mogą wykrywać potencjalne awarie zanim do nich dojdzie, co pozwala na proaktywne podejście do zarządzania ryzykiem.
Rola instrukcji obsługi i szkolenia
Oprócz technicznych aspektów bezpieczeństwa, kluczowe jest również odpowiednie przeszkolenie pracowników i dostarczenie im jasnych instrukcji obsługi. Szkolenia powinny obejmować zarówno teoretyczne, jak i praktyczne aspekty obsługi maszyn, w tym postępowanie w sytuacjach awaryjnych.
Bezpieczeństwo maszyn jest złożonym i wieloaspektowym zagadnieniem, które wymaga holistycznego podejścia. Kluczowe jest przestrzeganie regulacji, przeprowadzanie audytów, odpowiednie projektowanie i zarządzanie projektami, a także korzystanie z nowoczesnych technologii i outsourcingu inżynierów. Tylko kompleksowe podejście do bezpieczeństwa maszyn może zapewnić bezpieczne i efektywne środowisko pracy w nowoczesnym przemyśle.
Zarządzanie bezpieczeństwem maszyn wymaga współpracy między różnymi działami### Bezpieczeństwo maszyn: Kluczowe aspekty i najlepsze praktyki
FAQ: Bezpieczeństwo maszyn
Bezpieczeństwo maszyn odnosi się do zestawu środków i praktyk mających na celu zapobieganie wypadkom i minimalizację ryzyka związanego z użytkowaniem maszyn.
Bezpieczeństwo maszyn odnosi się do zestawu środków i praktyk mających na celu zapobieganie wypadkom i minimalizację ryzyka związanego z użytkowaniem maszyn.
Kluczowe regulacje to Dyrektywa Maszynowa 2006/42/WE oraz Dyrektywa Narzędziowa 2009/104/WE, które określają wymagania dotyczące projektowania, produkcji i użytkowania maszyn.
Procedura oceny zgodności to formalny proces, w którym maszyny są oceniane pod kątem zgodności z odpowiednimi normami i przepisami, aby mogły być oznakowane znakiem CE.
Ocena ryzyka maszyn obejmuje identyfikację potencjalnych zagrożeń, ocenę ryzyka z nimi związanego oraz wdrożenie środków zapobiegawczych, aby zminimalizować ryzyko.
Wymagania minimalne obejmują bezpieczeństwo konstrukcji, regularne przeglądy i konserwację, dostarczanie instrukcji obsługi oraz zapewnienie odpowiednich środków ochrony indywidualnej.
Certyfikacja CE potwierdza, że maszyna spełnia wszystkie wymagania bezpieczeństwa określone w dyrektywach UE, co umożliwia jej legalne wprowadzenie na rynek.
Automatyka przemysłowa może zwiększać wydajność, ale wprowadza również nowe zagrożenia, które wymagają odpowiednich środków zapobiegawczych i procedur bezpieczeństwa.
Audyty bezpieczeństwa maszyn pomagają zidentyfikować potencjalne zagrożenia i wdrożyć odpowiednie środki zapobiegawcze, co minimalizuje ryzyko wypadków i awarii.
Przemysł 4.0, z technologiami takimi jak IoT i sztuczna inteligencja, wprowadza nowoczesne systemy monitorowania i diagnostyki, które mogą znacznie poprawić bezpieczeństwo maszyn.
analiza ryzyka automatyka przemysłowa automatyzacja procesów produkcyjnych automatyzacja produkcji bezpieczeństwo maszyn deklaracja zgodności WE dokumentacja techniczna dostosowanie maszyn do wymagań minimalnych dyrektywa ATEX dyrektywa EMC dyrektywa LVD dyrektywa maszynowa 2006/42/WE GPSD GPSR hazop Instrukcja obsługi integrator automatyki przemysłowej inżynieria procesowa KPI linie produkcyjne maszyna nieukończona mes normy zharmonizowane ocena ryzyka OEE oznakowanie CE Performence level poka-yoke pokrycie diagnostyczne projektowanie maszyn przemysł spożywczy roboty przemysłowe rozporządzenie w sprawie maszyn 2023/1230 sat SCADA SIL smed stanowiska zrobotyzowane TPM zarządzanie zarządzanie projektami Znak CE
Zobacz także:
Napisz do nas!
Chętnie odpowiemy na Twoje pytania!