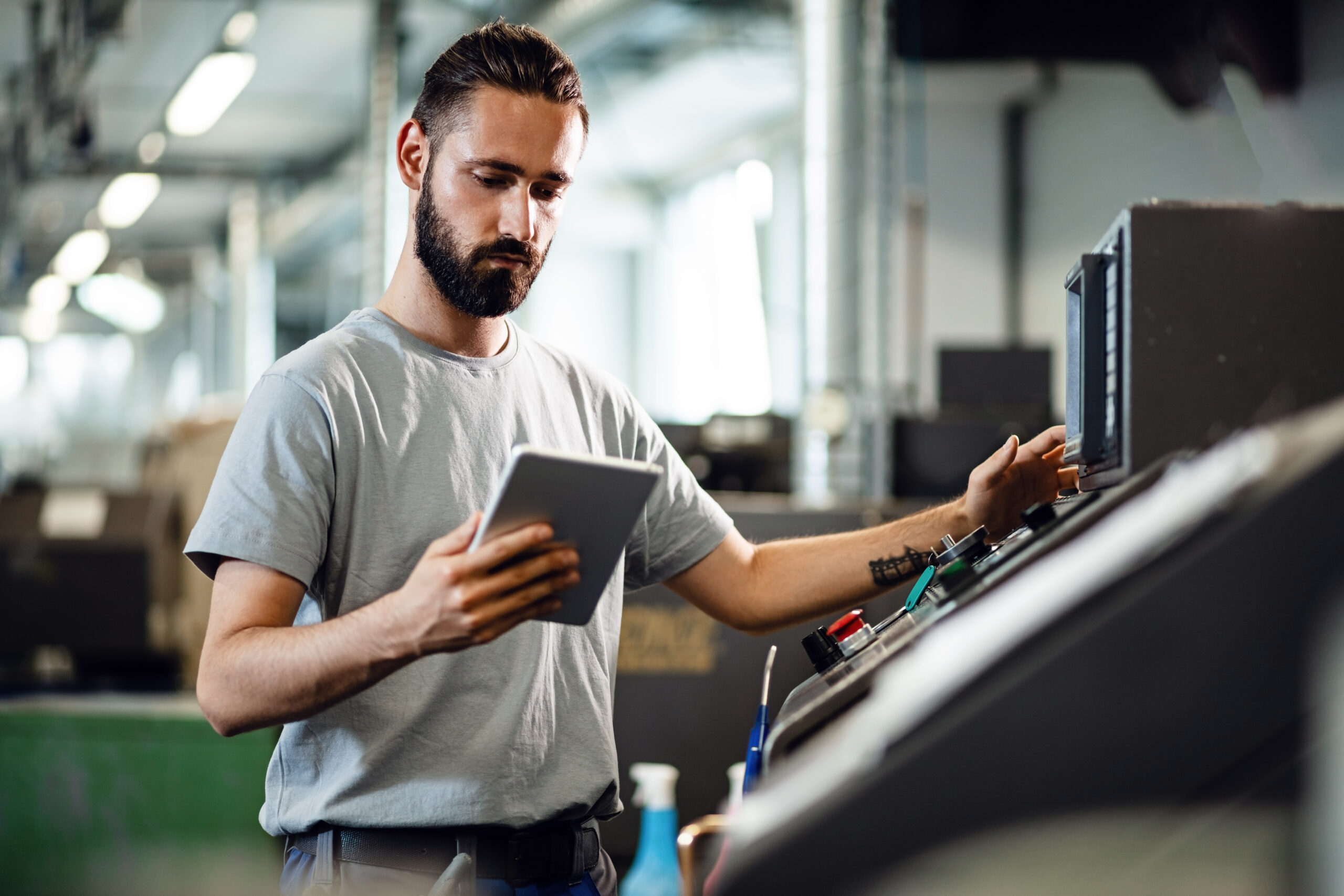
W środowisku przemysłowym, gdzie maszyny działają z dużymi siłami i prędkościami, bezpieczeństwo operatorów jest absolutnym priorytetem. Sterowanie dwuręczne (Two-Hand Control Devices, THCD) to mechanizm zaprojektowany w celu eliminacji ryzyka przypadkowego uruchomienia maszyn i kontaktu z ich ruchomymi częściami. Zgodnie z normą ISO 13851:2019, urządzenia te wymuszają jednoczesne zaangażowanie obu rąk operatora, co skutecznie minimalizuje ryzyko wypadków.
W artykule omówimy, jak powinno działać sterowanie dwuręczne zgodnie z normami, przedstawimy techniczne aspekty jego budowy oraz najczęstsze błędy implementacyjne.
Spis Treści
Typy urządzeń dwuręcznego sterowania – jak wybrać odpowiednie rozwiązanie?
Sterowanie dwuręczne to mechanizm, który zmusza operatora do użycia obu rąk jednocześnie, aby uruchomić maszynę. Dzięki temu ryzyko przypadkowego kontaktu z ruchomymi elementami jest znacznie ograniczone. Norma ISO 13851 dokładnie opisuje wymagania dla takich systemów i dzieli je na trzy typy, zależnie od poziomu bezpieczeństwa, jaki mają zapewniać.
Jakie są typy sterowania dwuręcznego?
Typ I – podstawowe zabezpieczenie
To rozwiązanie o najniższym poziomie bezpieczeństwa (PL c/SIL 1). W tym przypadku:
- Nie ma wymogu synchronizacji przycisków – można je wcisnąć w różnym czasie.
- Nie jest wymagana ponowna inicjalizacja – możliwe jest uruchomienie maszyny przez pojedyncze naciśnięcie po zwolnieniu.
Gdzie stosować?
Maszyny o niskim ryzyku, gdzie inne zabezpieczenia minimalizują zagrożenie, np. osłony stałe. Przykład: urządzenia montażowe o ograniczonej sile i prędkości.
Typ II – lepsza ochrona
Ten typ oferuje wyższy poziom bezpieczeństwa (PL d/SIL 2) i wprowadza dodatkowe wymagania:
- Nie wymaga synchronizacji czasowej między naciśnięciami.
- Operator musi zwolnić oba przyciski i ponownie je wcisnąć, aby uruchomić maszynę (wymóg ponownej inicjalizacji).
Gdzie stosować?
Maszyny o umiarkowanym ryzyku, np. prasy średniej wielkości, gdzie ryzyko kontaktu z narzędziem jest większe, ale skutki urazu nie są krytyczne.
Typ III – maksymalne bezpieczeństwo
Najwyższy poziom ochrony zapewnia typ III (PL e/SIL 3), który wprowadza:
- Synchronizację czasową – oba przyciski muszą być wciśnięte w ciągu 0,5 sekundy.
- Wymóg ponownej inicjalizacji – po zwolnieniu jednego z przycisków konieczne jest ponowne wciśnięcie obu.
Podtypy:
- IIIA: Prostsza konfiguracja (styki przycisków połączone szeregowo), co ogranicza diagnostykę.
- IIIC: Każdy przycisk jest podłączony niezależnie, co zapewnia lepszą wykrywalność błędów.
Gdzie stosować?
Maszyny wysokiego ryzyka, takie jak prasy o dużej sile, krawędziarki czy młoty przemysłowe. Typ IIIC sprawdza się tam, gdzie niezawodność i precyzyjna diagnostyka bezpieczeństwa jest wymogiem analizy ryzyka.
Co wybrać?
Dobór odpowiedniego typu sterowania dwuręcznego zależy od:
- Oceny ryzyka: Jakie zagrożenia występują przy pracy maszyny?
- Charakterystyki maszyny: Jakie są prędkości, siły i sposób obsługi?
- Wymagań funkcjonalnych: Czy potrzebna jest synchronizacja i ponowna inicjalizacja?
Przykładowo, maszyna o wysokiej prędkości ruchomych części i dużej sile, taka jak prasa przemysłowa, powinna mieć sterowanie dwuręczne typu IIIC, które zapewnia najwyższy poziom bezpieczeństwa.
Norma ISO 13851:2019 jasno określa wymagania dla urządzeń dwuręcznego sterowania, dostosowując je do różnych poziomów ryzyka. Ostateczny wybór typu zależy od specyfiki maszyny i wyników oceny ryzyka. Jeśli chodzi o bezpieczeństwo, nie ma miejsca na kompromisy – odpowiednie dobranie systemu sterowania dwuręcznego to podstawa ochrony operatorów w przemyśle.
Jeśli potrzebujesz pomocy w dopasowaniu systemu do swojej aplikacji, zawsze możesz liczyć na wsparcie. Wspólnie znajdziemy najlepsze rozwiązanie.
Status prawny
Zgodnie z Dyrektywą maszynową 2006/42/WE (Załącznik V) oraz Rozporządzeniem maszynowym 2023/1230 (Załącznik II), pulpity dwuręczne są uznawane za elementy bezpieczeństwa. Muszą spełniać określone wymagania techniczne oraz podlegać procedurom oceny zgodności. Chociaż nie są stricte maszyną podlegają pod wymagania zasadnicze!
Procedura oceny zgodności
Jako urządzenia bezpieczeństwa pulpity dwuręczne podlegają badaniu typu UE (moduł B) oraz wewnętrznej kontroli produkcji (moduł C). Po zakończeniu oceny producent umieszcza znak CE, co potwierdza zgodność produktu z przepisami i wymaganiami bezpieczeństwa. Pulpity dwuręczne pełnią istotną rolę w ochronie operatorów i dzięki zgodności z normami oraz przepisami prawnymi są niezawodnym rozwiązaniem w zastosowaniach przemysłowych.
Integracja sterowania dwuręcznego z czasem dobiegu maszyny
Czas dobiegu maszyny to istotny parametr, który należy uwzględnić przy projektowaniu maszyn i systemów bezpieczeństwa. Norma PN-EN ISO 13855 precyzuje, że odległość między operatorem a strefą zagrożenia musi być tak dobrana, aby maszyna zdążyła się zatrzymać, zanim operator dotrze do niebezpiecznych elementów. Uwzględnia się przy tym czas reakcji systemu oraz prędkość zbliżania się dłoni operatora.
Przykład:
- Czas dobiegu maszyny: 300 ms (0,3 s).
- Prędkość zbliżania się dłoni operatora: 2 m/s (zgodnie z normą PN-EN ISO 13855).
- Minimalna odległość od strefy zagrożenia: d=t×v=0,3 s×2 m/s=0,6 m
Przyciski sterowania dwuręcznego muszą być rozmieszczone w taki sposób, aby strefa zagrożenia znajdowała się co najmniej 600 mm od operatora. To gwarantuje, że maszyna zatrzyma się, zanim operator będzie miał szansę dotknąć jej niebezpiecznych części.
Sterowanie dwuręczne w różnych środowiskach – energia elektryczna i pneumatyczna
Norma ISO 13851 odnosi się do urządzeń dwuręcznego sterowania (THCD) niezależnie od ich źródła energii, co oznacza, że mogą być one projektowane zarówno w wersji elektrycznej, jak i pneumatycznej. Wybór odpowiedniego rodzaju zasilania zależy od warunków pracy maszyny, w tym specyficznych wymagań dotyczących środowisk zagrożonych wybuchem (ATEX).
Pneumatyczne sterowanie dwuręczne to rozwiązanie idealne dla maszyn pracujących w trudnych warunkach środowiskowych, takich jak wysoka wilgotność, zapylenie czy atmosfery zagrożone wybuchem (ATEX). Dzięki eliminacji elementów elektrycznych systemy te minimalizują ryzyko iskrzenia, co czyni je niezastąpionymi w środowiskach EX, np. w przemyśle chemicznym i petrochemicznym. Prosta konstrukcja oparta na zaworach 3/2, logicznych „AND” i hamulcach pneumatycznych zapewnia niezawodność działania, nawet w ekstremalnych warunkach.
FAQ: Sterowanie dwuręczne
Nie ma obowiązku stosowania norm zharmonizowanych, jednak ich stosowanie zapewnia domniemanie zgodności z wymaganiami zasadniczymi. Jeśli jej nie stosujemy musimy wykazać inne rozwiązanie zapewniające wystarczający poziom bezpieczeństwa. Norma określa wymagania projektowe, funkcjonalne i klasyfikację na trzy typy urządzeń w zależności od poziomu bezpieczeństwa (PL/SIL)
W urządzeniach typu III oba przyciski muszą zostać wciśnięte w czasie nie dłuższym niż 0,5 sekundy. Jeśli ten czas zostanie przekroczony, urządzenie nie wygeneruje sygnału wyjściowego i wymagana będzie ponowna inicjalizacja.
Tak, w strefach zagrożonych wybuchem najlepiej sprawdzają się pneumatyczne systemy sterowania dwuręcznego. Dzięki eliminacji elementów elektrycznych minimalizują ryzyko iskrzenia, co czyni je bezpiecznym wyborem w środowiskach EX.
Typ I oferuje podstawowe zabezpieczenie bez synchronizacji i ponownej inicjalizacji (PL c/SIL 1). Typ II wymaga ponownej inicjalizacji, ale nie synchronizacji (PL d/SIL 2). Typ III zapewnia najwyższe bezpieczeństwo z synchronizacją (≤0,5 s) i ponowną inicjalizacją (PL e/SIL 3).
Dobór systemu zależy od oceny ryzyka, specyfiki maszyny i środowiska pracy. Maszyny wysokiego ryzyka, takie jak prasy przemysłowe, wymagają systemów typu III, które zapewniają najwyższy poziom ochrony operatora.
analiza ryzyka automatyka przemysłowa automatyzacja procesów produkcyjnych automatyzacja produkcji bezpieczeństwo maszyn dokumentacja techniczna dyrektywa ATEX dyrektywa EMC dyrektywa maszynowa 2006/42/WE Instrukcja obsługi integrator automatyki przemysłowej KPI maszyna nieukończona normy zharmonizowane OEE oznakowanie CE Performence level projektowanie maszyn rozporządzenie w sprawie maszyn 2023/1230 Znak CE
Zobacz także:
Napisz do nas!
Chętnie odpowiemy na Twoje pytania!