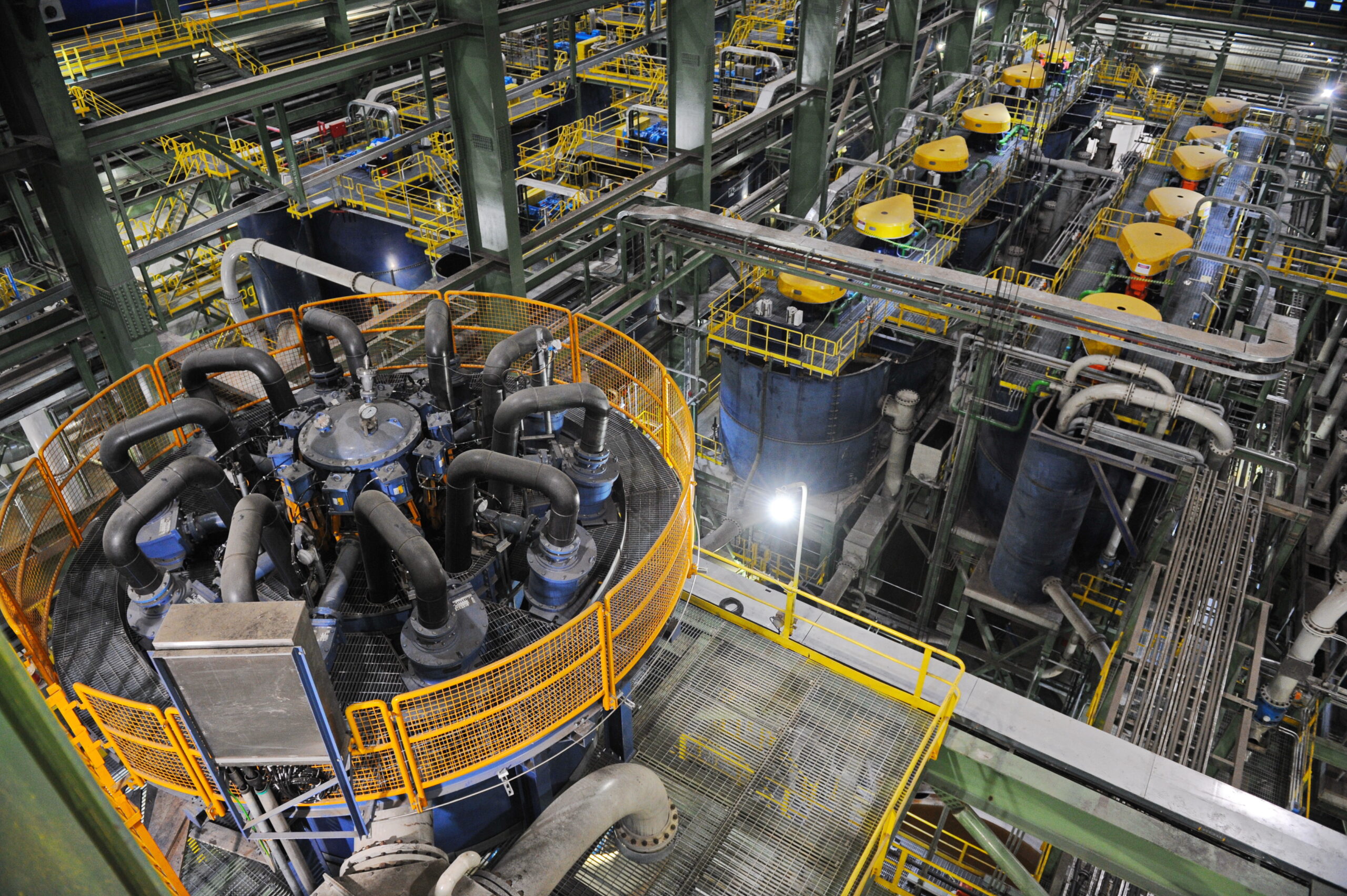
Czy zastanawiałeś się, jak poważne mogą być skutki wybuchu w zakładzie produkcyjnym, jeśli nie przeprowadzisz rzetelnej oceny ryzyka? Błędy na tym etapie mogą grozić nie tylko przestojem linii technologicznej, lecz przede wszystkim zagrożeniem zdrowia i życia pracowników. Poniżej przedstawiamy praktyczne spojrzenie na ocenę ryzyka wybuchu w oparciu o PN-EN ISO 1127-1, ze wskazaniem, jak wpisuje się ona w wymagania dyrektywy ATEX, maszynowej oraz Rozporządzenia UE 2023/1230.
Spis Treści
Ocena ryzyka wybuchu wg. PN-EN ISO 1127-1
Norma PN-EN ISO 1127-1 (zharmonizowana norma z ATEX) precyzuje, w jaki sposób należy przeprowadzić analizę i szacowanie ryzyka związanego z potencjalnymi atmosferami wybuchowymi. Stanowi ona zarazem podstawę do spełnienia wymagań europejskich dyrektyw, zwłaszcza:
- Dyrektywy ATEX (2014/34/UE), która reguluje urządzenia i systemy ochronne w przestrzeniach zagrożonych wybuchem.
- Dyrektywy maszynowej (2006/42/WE), w obszarze bezpieczeństwa maszyn, również uwzględniając aspekty przeciwwybuchowe.
- Rozporządzenia 2023/1230, które wprowadza nowe wymagania w zakresie projektowania i eksploatacji maszyn, w tym bezpieczeństwa związanego z wybuchami.
Jak zatem przełożyć te przepisy na praktyczne działania w przedsiębiorstwie?
Szkolenie
Dyrektywa Maszynowa
2006/42/WE
Zdobądź niezbędną wiedzę o Dyrektywie Maszynowej 2006/42/WE! Zarejestruj się na nasze szkolenie i zapewnij bezpieczeństwo w swoim zakładzie!
Jak wygląda taka ocena ryzyka wybuchu?
Zdefiniowanie zakresu i warunków procesu
Zaczynamy od dokładnego rozpoznania, gdzie w instalacji występują substancje palne (pyły, gazy, pary). W ramach tej identyfikacji bierze się pod uwagę:
- właściwości materiałów (temperatura zapłonu, dolne i górne granice wybuchowości),
- warunki pracy maszyn (ciśnienie, temperatura),
- potencjalne źródła rozszczelnień.
Ustalenie prawdopodobieństwa i skutków
Kolejno szacujemy, jak często może dojść do wystąpienia niebezpiecznej atmosfery wybuchowej i z jakimi konsekwencjami się to wiąże. Im większa częstotliwość, tym wyższe wymagania stawiane urządzeniom (kategorie ATEX, np. 1, 2 lub 3).
Opracowanie strategii bezpieczeństwa
Na bazie wyników oceny ryzyka tworzymy plan działań:
- projektujemy systemy, które ograniczają skutki ewentualnego wybuchu (odciążenie, tłumienie, izolowanie).
- ograniczamy substancje wybuchowe lub nadzorujemy ich stężenie poza zakresem wybuchowości,
- eliminujemy lub zabezpieczamy możliwe źródła zapłonu,
Ocena ryzyka wybuchu: Identyfikacja zagrożeń
Pierwszym krokiem jest zawsze mapowanie potencjalnych źródeł substancji palnych (gazów, par, mgieł lub pyłów). Zgodnie z PN-EN ISO 1127-1, w każdym punkcie procesu należy się zastanowić, czy istnieje możliwość powstania niebezpiecznej atmosfery wybuchowej. Uwzględniamy przy tym:
- warunki procesu technologicznego (np. temperatura, ciśnienie),
- właściwości chemiczne i fizyczne substancji,
- występowanie miejsc potencjalnych nieszczelności (połączenia kołnierzowe, zawory, uszczelki),
- strefy, w których może dochodzić do zakłóceń czy awarii (np. wadliwe działanie systemu wentylacji).
Im bardziej szczegółowo przeanalizujemy możliwe źródła zagrożeń, tym trafniejsza będzie ocena ryzyka.
Ocena ryzyka wybuchu: Rola zapłonu
Nawet jeżeli w systemie pojawi się mieszanka wybuchowa, do wybuchu wciąż niezbędny jest czynnik zapalający. Dyrektywa ATEX wymaga szczegółowej oceny i wyeliminowania (lub zminimalizowania) możliwych źródeł zapłonu, takich jak:
- gorące powierzchnie (np. elementy maszyn o podwyższonej temperaturze),
- iskry mechaniczne (tarcie, uderzenia),
- elektryczność statyczna,
- urządzenia elektryczne,
- wyładowania atmosferyczne,
- niewłaściwe prace spawalnicze.
Zgodnie z dyrektywą maszynową i nowym rozporządzeniem ws. maszyn 2023/1230, analiza tych zagrożeń musi być wbudowana już na etapie projektowania maszyny i uwzględniona w dokumentacji technicznej.
Jak podejść do analizy źródeł zapłonu?
W praktyce stosuje się tu kilka kroków:
- Lista kontrolna (tzw. check-lista)
Ustalamy wszystkie możliwe sposoby powstania iskry czy lokalnego przegrzania (np. w łożyskach, paskach klinowych, urządzeniach elektrycznych). - Klasyfikacja stref zagrożenia wybuchem
Na podstawie częstotliwości i czasu trwania występowania atmosfery wybuchowej. Ma to bezpośrednie przełożenie na dobór zabezpieczeń i kategorii urządzeń (np. ATEX kategoria 1, 2 lub 3). - Zastosowanie odpowiednich norm
Poza PN-EN ISO 1127-1, istotne są np. normy z serii EN 60079 dotyczące urządzeń elektrycznych i metod ochrony (iskrobezpieczeństwo, budowa przeciwwybuchowa itp.). - Weryfikacja i testy
M.in. pomiary rezystancji uziemień, kontrola temperatury powierzchni, pomiary stężeń gazów lub pyłów.
Redukcja ryzyka wybuchu – praktyczne rozwiązania
Skuteczne obniżenie ryzyka do akceptowalnego poziomu wymaga najczęściej połączenia kilku metod:
- Eliminacja substancji palnych lub ich ograniczenie
Poprzez zmianę technologii, utrzymanie stężenia poniżej granic wybuchowości albo stosowanie inertyzacji (np. azotem). - Zapobieganie emisjom i nieszczelnościom
Dobre praktyki projektowe, stosowanie dodatkowych uszczelnień czy monitorowanie potencjalnych punktów wycieku. - Unikanie źródeł zapłonu
Stosowanie urządzeń z oznaczeniem Ex, systemów antyelektrostatycznych, a także szkoleń z zakresu bezpiecznego wykonywania prac gorących (spawalniczych, szlifierskich). - Ograniczanie skutków wybuchu
W tym m.in. odciążanie wybuchu, tłumienie płomienia, izolowanie wybuchu czy konstrukcja odporna na wybuch. - Szkolenia i procedury
Personel musi znać ryzyka, procedury awaryjne i właściwe zasady konserwacji maszyn, tak by nie doprowadzać do sytuacji sprzyjających wybuchowi.
Ocena ryzyka wybuchu: Jak w praktyce wdrożyć wymogi i uniknąć błędów?
Wymagania stawiane przez dyrektywy (ATEX, maszynową) i PN-EN ISO 1127-1 mogą wydawać się złożone, szczególnie w kontekście rozporządzenia 2023/1230, które dodatkowo zaostrza pewne wytyczne. Jeśli potrzebujesz wsparcia przy:
- tworzeniu dokumentacji i analizie ryzyka wybuchu,
- wdrożeniu systemów zabezpieczających,
- doborze urządzeń zgodnych z ATEX,
- szkoleniach operatorów i kadry inżynieryjnej,
warto skorzystać z fachowej pomocy specjalistów.
Engineering Shield oferuje kompleksowe usługi doradcze oraz szkoleniowe w zakresie oceny ryzyka wybuchu i dostosowania maszyn do aktualnych przepisów. Dzięki naszym ekspertom unikniesz kosztownych przestojów i sankcji, a przede wszystkim zadbasz o bezpieczeństwo pracowników i infrastruktury.
Ocena ryzyka wybuchu wg. PN-EN ISO 1127-1 to nie tylko wymóg formalny, ale realne narzędzie do ochrony ludzi i majątku. Właściwa identyfikacja zagrożeń, analiza źródeł zapłonu i odpowiednie środki redukujące ryzyko powinny być fundamentem każdej instalacji czy procesu z substancjami palnymi. Pamiętajmy, że skuteczne wdrożenie tych rozwiązań wymaga zarówno wiedzy technicznej, jak i świadomości regulacyjnej — warto więc korzystać ze wsparcia doświadczonych partnerów.
FAQ: Ocena ryzyka wybuchu
Tak. Jeśli w Twojej firmie występują substancje palne (np. pyły, gazy, pary) i istnieje potencjalna możliwość wytworzenia atmosfer wybuchowych, przeprowadzenie oceny ryzyka wybuchu jest obowiązkowe. Dokument PN-EN ISO 1127-1 ułatwia zgodność z dyrektywą ATEX, dyrektywą maszynową oraz nowym Rozporządzeniem 2023/1230.
Czas oraz koszt zależą głównie od wielkości instalacji, stopnia skomplikowania procesów oraz rodzaju substancji palnych. Podczas pierwszej rozmowy oceniamy skalę przedsięwzięcia, a następnie proponujemy harmonogram i kosztorys dopasowany do potrzeb Twojego przedsiębiorstwa.
Bezpieczeństwo ludzi i mienia: ograniczasz ryzyko wypadków i awarii, które mogą prowadzić do strat materialnych i wizerunkowych.
Zgodność z przepisami: unikasz kar finansowych i problemów związanych z kontrolami organów nadzoru.
Sprawność operacyjna: prawidłowo zaprojektowane i utrzymywane instalacje rzadziej ulegają awariom, co przekłada się na mniejsze przestoje.
Możesz samodzielnie przygotować część danych (np. informacje o procesach, dokumentację maszyn), ale pełna ocena zwykle wymaga wiedzy specjalistycznej, w tym znajomości aktualnych norm, dyrektyw ATEX i maszynowej oraz Rozporządzenia 2023/1230. Współpraca z doświadczonym doradcą lub firmą inżynierską (taką jak Engineering Shield) pozwala przeprowadzić analizę rzetelnie i efektywnie.
Klasyfikacja stref zagrożenia wybuchem i dobór urządzeń o odpowiedniej kategorii ATEX.
Zastosowanie metod ograniczających skutki wybuchu, np. odciążenie, tłumienie czy izolowanie wybuchu.
Zapewnienie środków eliminujących źródła zapłonu, np. eliminacja iskrzenia, elektryczność statyczna, gorące powierzchnie.
Stworzenie procedur organizacyjnych (szkolenia, instrukcje konserwacji) zapewniających długotrwałe bezpieczeństwo.
analiza ryzyka automatyka przemysłowa automatyzacja procesów produkcyjnych automatyzacja produkcji bezpieczeństwo maszyn dokumentacja techniczna dyrektywa ATEX dyrektywa EMC dyrektywa maszynowa 2006/42/WE Instrukcja obsługi integrator automatyki przemysłowej KPI maszyna nieukończona normy zharmonizowane OEE oznakowanie CE Performence level projektowanie maszyn rozporządzenie w sprawie maszyn 2023/1230 Znak CE
Zobacz także:
Napisz do nas!
Chętnie odpowiemy na Twoje pytania!