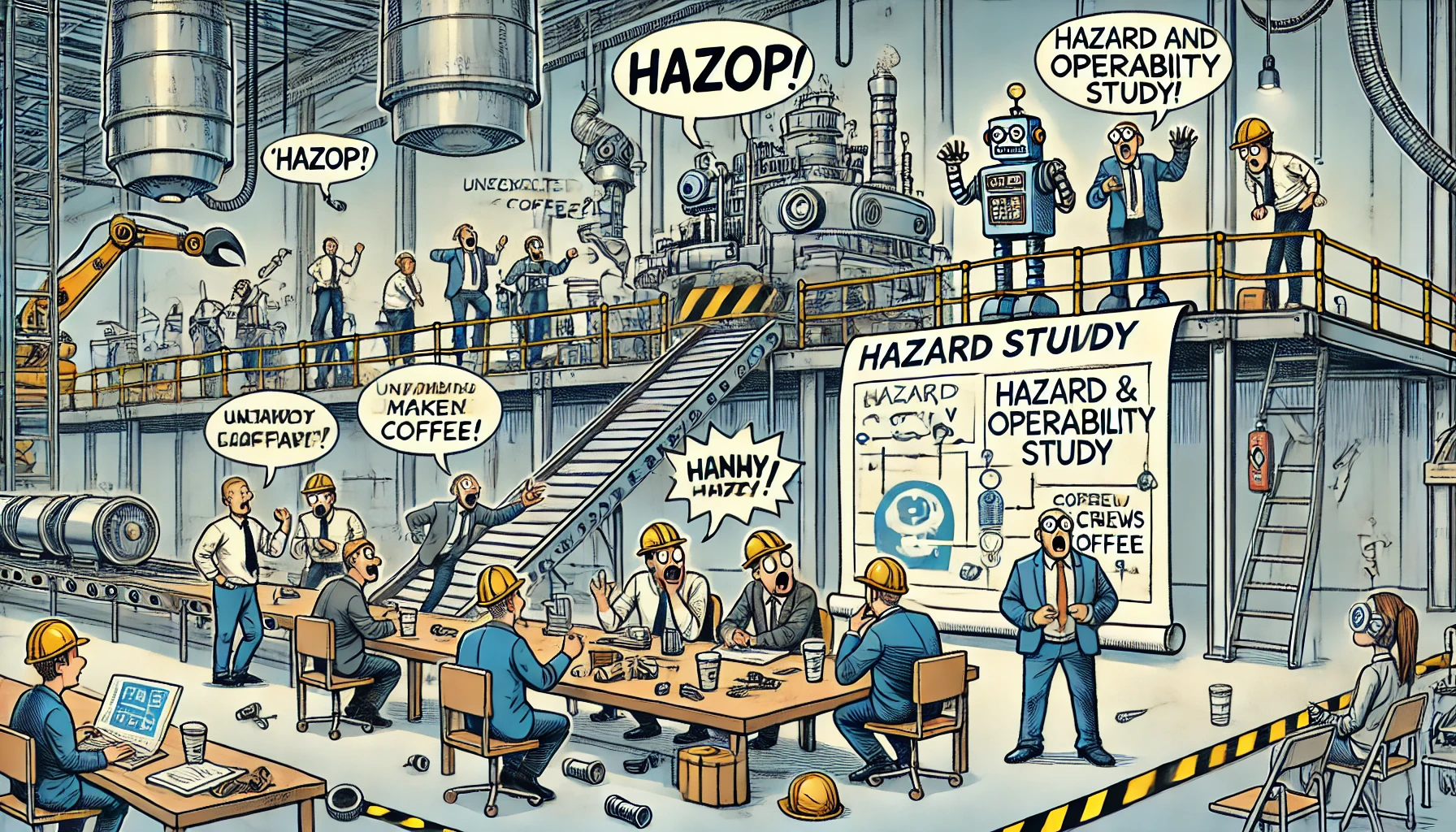
W dzisiejszym dynamicznie rozwijającym się świecie automatyki przemysłowej, zapewnienie bezpieczeństwa operacyjnego i identyfikacja potencjalnych zagrożeń staje się priorytetem dla firm. Jedną z najbardziej skutecznych metod analizy ryzyka i operacyjności systemów jest HAZOP (Hazard and Operability Study). Jest to systematyczne narzędzie używane do identyfikacji zagrożeń oraz potencjalnych problemów operacyjnych w projektach automatyki przemysłowej, projektowaniu maszyn i linii produkcyjnych. W niniejszym artykule przyjrzymy się bliżej metodzie HAZOP, jej znaczeniu w różnych dziedzinach oraz roli, jaką odgrywa w zapewnieniu zgodności z normami i dyrektywami, takimi jak Dyrektywa Maszynowa 2006/42/WE oraz certyfikacja CE.
Spis Treści
Czym jest HAZOP?
HAZOP to skrót od „Hazard and Operability Study”, czyli badania zagrożeń i zdolności operacyjnych. Jest to strukturalna i systematyczna technika stosowana do badania systemów w celu identyfikacji potencjalnych zagrożeń i problemów operacyjnych. Głównym celem HAZOP jest zrozumienie, jak i dlaczego system może odbiegać od zamierzonego działania oraz jakie mogą być tego konsekwencje.
Norma PN-EN 61882:2016-07E i HAZOP
Zakres Normy
Norma PN-EN 61882:2016-07E jest europejską normą określającą zasady przeprowadzania badań Hazard and Operability Study. Opisuje ona szczegółowo procedury, które powinny być stosowane podczas analizy ryzyka i operacyjności systemów. Norma ta wprowadza wymagania dla HAZOP w kontekście identyfikacji zagrożeń oraz oceny ryzyka w różnych fazach cyklu życia systemu.
Kluczowe Elementy Normy
- Podział Systemu na Części:
- System powinien być podzielony na mniejsze części, które można dokładnie analizować. Wielkość tych części zależy od złożoności systemu oraz potencjalnych skutków ryzyka. W prostych systemach części mogą być większe, natomiast w złożonych systemach powinny być mniejsze, aby umożliwić szczegółową analizę.
- Właściwości Projektowe:
- Intencje projektowe są wyrażone w kategoriach właściwości, które przekazują istotne cechy części systemu. Te właściwości mogą obejmować wejścia i wyjścia, funkcje, aktywności oraz źródła i cele. Przykładowo, w systemie chemicznym właściwości mogą obejmować temperaturę, ciśnienie i skład chemiczny.
- Słowa Kluczowe:
- Analiza Hazard and Operability Study wykorzystuje zestaw słów kluczowych, które służą do identyfikacji potencjalnych odchyleń od zamierzeń projektowych. Przykłady słów kluczowych to: „Brak”, „Więcej”, „Mniej”, „Część”, „Odwrotność”, „Inny niż”, „Wcześniej”, „Później”, „Przed”, „Po”. Słowa te pomagają zespołowi w systematycznym przeszukiwaniu wszystkich aspektów systemu.
- Przykłady Zastosowania:
- Norma zawiera szereg przykładów zastosowania HAZOP w różnych kontekstach, w tym w systemach procesowych, systemach transportowych, systemach programowalnych oraz procedurach administracyjnych. Przykłady te ilustrują, jak analiza HAZOP może być stosowana do identyfikacji zagrożeń i problemów operacyjnych w różnych branżach.
Proces Przeprowadzania Analizy HAZOP zgodnie z Normą
- Inicjacja Badania:
- Badanie HAZOP rozpoczyna się od wyznaczenia lidera badania oraz zespołu specjalistów z różnych dziedzin, takich jak inżynieria, bezpieczeństwo, operacje i zarządzanie. Lider badania jest odpowiedzialny za koordynację całego procesu oraz zapewnienie, że wszystkie etapy są przeprowadzone zgodnie z normą.
- Określenie Zakresu i Celów:
- Lider badania, we współpracy z zespołem, określa zakres analizy oraz jej cele. Obejmuje to identyfikację wszystkich elementów systemu, które będą poddane analizie, oraz wyznaczenie kryteriów, na podstawie których będą oceniane potencjalne zagrożenia. Zakres badania powinien uwzględniać granice systemu oraz jego interfejsy z innymi systemami i środowiskiem zewnętrznym.
- Przygotowanie:
- Zespół zbiera wszystkie niezbędne dane i dokumentacje dotyczące systemu, w tym schematy, opisy funkcjonalne, procedury operacyjne i instrukcje obsługi. Na podstawie tych informacji przygotowywane są szczegółowe opisy intencji projektowych. Lider badania zapewnia, że wszystkie informacje są kompletne i dokładne, co jest kluczowe dla skuteczności analizy.
- Przeprowadzenie Analizy:
- Analiza Hazard and Operability Study jest przeprowadzana za pomocą zestawu słów kluczowych, które służą do identyfikacji potencjalnych odchyleń od zamierzeń projektowych. Każde odchylenie jest analizowane pod kątem przyczyn, skutków oraz możliwych działań korygujących. Zespół badawczy systematycznie przechodzi przez wszystkie części systemu, stosując słowa kluczowe do każdego zidentyfikowanego odchylenia.
- Dokumentacja i Działania Następcze:
- Wyniki analizy są szczegółowo dokumentowane, a lider badania zapewnia, że wszystkie zidentyfikowane zagrożenia są odpowiednio zarządzane. Na podstawie wyników analizy podejmowane są działania korygujące, mające na celu eliminację lub minimalizację ryzyka. Dokumentacja powinna zawierać szczegółowe opisy zidentyfikowanych zagrożeń, przyczyn, skutków oraz rekomendowanych działań naprawczych.
1. Taśmociąg transportujący części
Element systemu | Intencja projektowa | Słowo kluczowe | Odchylenie | Przyczyny | Skutki | Zalecenia |
---|---|---|---|---|---|---|
Taśmociąg | Transport części z punktu A do punktu B | Brak | Brak ruchu taśmociągu | Awaria napędu, zablokowanie przez obiekt | Przerwanie produkcji, opóźnienia | Regularna konserwacja napędu, czujniki blokad |
Taśmociąg | Transport części z punktu A do punktu B | Więcej | Zbyt szybki ruch | Awaria sterownika, błędne ustawienia prędkości | Uszkodzenie części, ryzyko wypadków | Kontrola prędkości, kalibracja sterowników |
HAZOP w Kontekście Certyfikacji CE i Dyrektywy Maszynowej 2006/42/WE
Dyrektywa Maszynowa 2006/42/WE
Dyrektywa Maszynowa 2006/42/WE określa wymagania dotyczące bezpieczeństwa i ochrony zdrowia w odniesieniu do projektowania i budowy maszyn. Chociaż sama dyrektywa nie wymaga przeprowadzania analizy HAZOP, przeprowadzenie takiej analizy może znacząco przyczynić się do spełnienia wymogów dyrektywy. Dzięki HAZOP, producenci mogą zidentyfikować i ocenić potencjalne zagrożenia na etapie projektowania, co pozwala na wprowadzenie niezbędnych środków zapobiegawczych i korekcyjnych jeszcze przed wdrożeniem maszyny do użytku.
Analiza HAZOP pomaga w identyfikacji słabych punktów i potencjalnych problemów operacyjnych, które mogą nie być od razu widoczne podczas tradycyjnych procedur oceny ryzyka. Dzięki temu możliwe jest zwiększenie niezawodności i bezpieczeństwa maszyn, co z kolei prowadzi do lepszego spełnienia wymogów Dyrektywy Maszynowej oraz minimalizacji ryzyka awarii i wypadków.
Certyfikacja CE
Certyfikacja CE jest oznaczeniem, które potwierdza, że produkt spełnia wszystkie odpowiednie dyrektywy i normy Unii Europejskiej. Choć analiza Hazard and Operability Study nie jest wymagana do uzyskania certyfikacji CE, jej przeprowadzenie może znacząco wspomóc ten proces.
Przeprowadzenie analizy HAZOP umożliwia wykrycie potencjalnych zagrożeń i problemów na etapie projektowania i produkcji. Dzięki temu producenci mogą wdrożyć odpowiednie środki zaradcze, które zwiększą bezpieczeństwo i niezawodność maszyny. Analiza HAZOP pomaga również w przygotowaniu pełnej dokumentacji technicznej, która jest niezbędna do uzyskania certyfikacji CE.
Warto podkreślić, że certyfikacja CE to nie tylko spełnienie wymogów prawnych, ale również znak jakości i bezpieczeństwa, który zwiększa zaufanie klientów do produktów. Dzięki przeprowadzeniu analizy HAZOP, producenci mogą lepiej przygotować się do procesu certyfikacji, minimalizując ryzyko problemów na późniejszych etapach oraz zapewniając, że ich produkty są bezpieczne i niezawodne.
Przykłady Zastosowania HAZOP
Przemysł Chemiczny
W przemyśle chemicznym analiza HAZOP jest stosowana do oceny bezpieczeństwa procesów produkcyjnych, gdzie identyfikacja potencjalnych zagrożeń, takich jak wycieki chemikaliów czy eksplozje, jest kluczowa dla zapewnienia bezpieczeństwa pracowników i środowiska. Analiza Hazard and Operability Study pozwala na dokładne przeanalizowanie wszystkich etapów procesu produkcyjnego i zidentyfikowanie potencjalnych punktów awarii.
Przemysł Spożywczy
W przemyśle spożywczym HAZOP pomaga w identyfikacji zagrożeń związanych z jakością i bezpieczeństwem żywności. Analiza obejmuje każdy etap produkcji, od surowców po gotowy produkt, co pozwala na zapewnienie zgodności z normami i standardami bezpieczeństwa żywności. Dzięki HAZOP możliwe jest zidentyfikowanie potencjalnych zagrożeń, takich jak zanieczyszczenia krzyżowe, oraz zaplanowanie odpowiednich działań zapobiegawczych.
Przemysł Energetyczny
W sektorze energetycznym Hazard and Operability Study jest używany do oceny ryzyka związanego z eksploatacją instalacji energetycznych, takich jak elektrownie czy sieci przesyłowe. Analiza pozwala na identyfikację potencjalnych zagrożeń, takich jak awarie sprzętu czy błędy operacyjne, i zaplanowanie odpowiednich działań zapobiegawczych. Dzięki HAZOP możliwe jest zapewnienie ciągłości działania i minimalizacja ryzyka wystąpienia poważnych awarii.
Rola Outsourcingu Inżynierów w Procesie
W dzisiejszych czasach wiele firm decyduje się na outsourcing inżynierów do przeprowadzania analiz Hazard and Operability Study. Zewnętrzni specjaliści przynoszą ze sobą bogate doświadczenie i wiedzę, co pozwala na dokładniejszą i bardziej obiektywną ocenę ryzyka. Outsourcing inżynierów może być szczególnie korzystny w przypadkach, gdy firma nie dysponuje wystarczającymi zasobami lub kompetencjami do przeprowadzenia analizy we własnym zakresie.
HAZOP to nieocenione narzędzie w dziedzinie automatyki przemysłowej, które pozwala na systematyczne identyfikowanie zagrożeń i problemów operacyjnych. Dzięki zastosowaniu analizy HAZOP firmy mogą zapewnić zgodność z normami i dyrektywami, takimi jak Dyrektywa Maszynowa 2006/42/WE, oraz uzyskać certyfikację CE. Przeprowadzenie analizy HAZOP wymaga zaangażowania doświadczonych specjalistów i dokładnej dokumentacji, co pozwala na minimalizację ryzyka i zapewnienie bezpieczeństwa operacyjnego. Współpraca z zewnętrznymi inżynierami w ramach outsourcingu może dodatkowo zwiększyć efektywność i dokładność przeprowadzanych analiz.
Automatyka przemysłowa, projektowanie maszyn, certyfikacja CE, bezpieczeństwo maszyn, oraz wiele innych obszarów korzysta z metody HAZOP, co czyni ją kluczowym elementem współczesnych standardów bezpieczeństwa i jakości w przemyśle. Dzięki HAZOP możliwe jest nie tylko zapewnienie zgodności z wymaganiami prawnymi, ale także poprawa efektywności i niezawodności systemów przemysłowych.
FAQ: HAZOP
Odpowiedź: Analiza HAZOP (Hazard and Operability Study) to systematyczna technika służąca do identyfikacji zagrożeń i problemów operacyjnych w systemach przemysłowych. Proces ten polega na dokładnym badaniu różnych elementów systemu, aby zrozumieć, jak mogą one odbiegać od zamierzonego działania i jakie mogą być tego konsekwencje.
Odpowiedź: Proces HAZOP obejmuje cztery główne etapy: inicjację badania, określenie zakresu i celów, przygotowanie oraz przeprowadzenie analizy. Każdy etap jest kluczowy dla zapewnienia dokładności i skuteczności analizy.
Odpowiedź: Analiza HAZOP jest ważna, ponieważ pozwala na wczesne zidentyfikowanie potencjalnych zagrożeń i problemów operacyjnych, co umożliwia wprowadzenie niezbędnych środków zapobiegawczych i korekcyjnych. Dzięki temu można zwiększyć bezpieczeństwo i niezawodność systemów przemysłowych.
Odpowiedź: Analiza HAZOP nie jest bezpośrednio wymagana przez Dyrektywę Maszynową 2006/42/WE, ale jej przeprowadzenie może znacząco przyczynić się do spełnienia wymagań dyrektywy. HAZOP pomaga w identyfikacji zagrożeń na etapie projektowania, co zwiększa zgodność z wymogami dyrektywy.
Odpowiedź: Przeprowadzenie analizy HAZOP może wspierać proces certyfikacji CE, ponieważ umożliwia wykrycie potencjalnych zagrożeń i problemów na etapie projektowania i produkcji. To pozwala na wdrożenie odpowiednich środków zaradczych, które zwiększają bezpieczeństwo i niezawodność maszyny, co jest kluczowe dla uzyskania certyfikacji CE.
Odpowiedź: Korzyści z przeprowadzenia analizy HAZOP obejmują poprawę bezpieczeństwa operacyjnego, zwiększenie niezawodności systemów, identyfikację i eliminację potencjalnych zagrożeń oraz lepsze przygotowanie do procesu certyfikacji CE. Dodatkowo, HAZOP wspiera zgodność z normami i dyrektywami, takimi jak Dyrektywa Maszynowa 2006/42/WE.
Odpowiedź: Analiza HAZOP jest stosowana w wielu branżach, w tym w przemyśle chemicznym, spożywczym, energetycznym, farmaceutycznym i motoryzacyjnym. Każda branża, która korzysta z zaawansowanych systemów technologicznych i procesów produkcyjnych, może skorzystać z tej metody.
Odpowiedź: W przeprowadzanie analizy powinni być zaangażowani specjaliści z różnych dziedzin, w tym inżynierowie, eksperci ds. bezpieczeństwa, operacje oraz zarządzanie. Ważne jest, aby zespół był zróżnicowany i posiadał odpowiednie kompetencje do dokładnej analizy systemu.
Odpowiedź: Analiza HAZOP powinna być przeprowadzana na różnych etapach cyklu życia systemu, w tym na etapie projektowania, przed uruchomieniem, podczas eksploatacji oraz przed wprowadzeniem istotnych zmian. Regularne przeprowadzanie analizy pomaga w utrzymaniu wysokiego poziomu bezpieczeństwa i niezawodności.
Odpowiedź: Ograniczenia analizy obejmują zależność od kompetencji i doświadczenia zespołu badawczego, możliwość pominięcia niektórych zagrożeń w złożonych systemach oraz potrzebę integracji z innymi metodami analizy ryzyka, aby zapewnić pełne pokrycie wszystkich potencjalnych zagrożeń.
analiza ryzyka automatyka przemysłowa automatyzacja procesów produkcyjnych automatyzacja produkcji bezpieczeństwo maszyn deklaracja zgodności WE dokumentacja techniczna dostosowanie maszyn do wymagań minimalnych dyrektywa ATEX dyrektywa EMC dyrektywa LVD dyrektywa maszynowa 2006/42/WE Instrukcja obsługi integrator automatyki przemysłowej KPI linie produkcyjne maszyna nieukończona normy zharmonizowane ocena ryzyka OEE oznakowanie CE Performence level poka-yoke pokrycie diagnostyczne projektowanie maszyn przemysł spożywczy roboty przemysłowe rozporządzenie w sprawie maszyn 2023/1230 sat SCADA smed stanowiska zrobotyzowane TPM zarządzanie zarządzanie projektami Znak CE