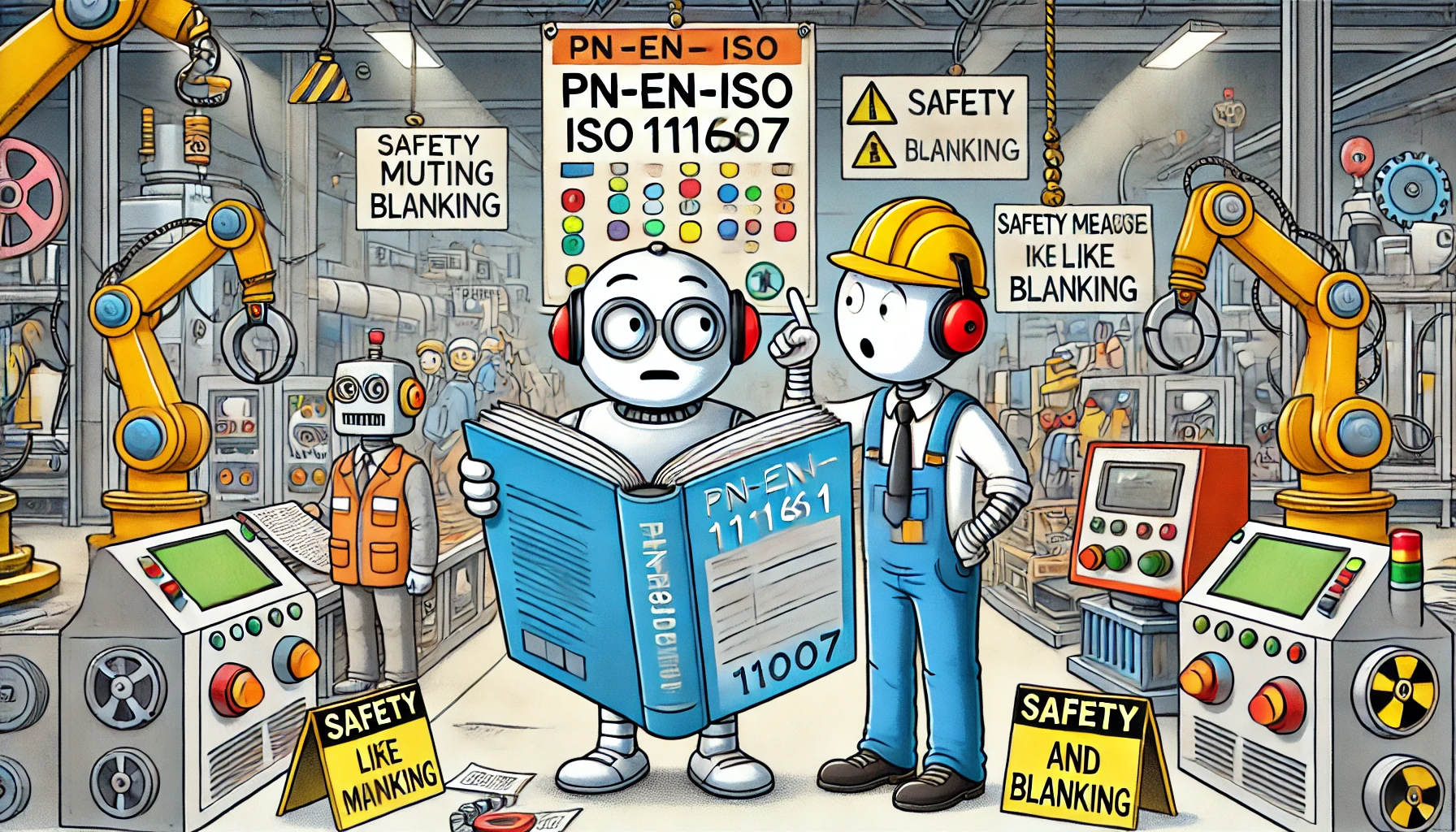
Norma PN-EN-ISO 11161 jest fundamentalnym dokumentem dla zapewnienia bezpieczeństwa w zintegrowanych systemach produkcyjnych. Jej celem jest zagwarantowanie, że skomplikowane systemy produkcyjne, składające się z wielu współpracujących maszyn, są projektowane i eksploatowane w sposób bezpieczny zarówno dla operatorów, jak i otoczenia. Poniżej przedstawiono najważniejsze aspekty tej normy, które są kluczowe dla projektantów maszyn oraz integratorów automatyki przemysłowej.
Spis Treści
Holistyczne podejście do bezpieczeństwa
Norma PN-EN-ISO 11161 podkreśla, że zintegrowany system produkcyjny powinien być traktowany jako całość, a nie jako zbiór pojedynczych elementów. Ocena ryzyka oraz wdrożenie środków ochronnych muszą obejmować cały system, uwzględniając interakcje między poszczególnymi maszynami. Takie podejście zapewnia kompleksową ochronę i minimalizuje ryzyko związane z nieprzewidzianymi interakcjami między różnymi komponentami systemu. W przypadku zintegrowanych systemów produkcyjnych, ryzyko może wynikać nie tylko z działania pojedynczych maszyn, ale również z ich wzajemnych oddziaływań. Dlatego też, ocena ryzyka musi być prowadzona na poziomie całego systemu, a nie tylko jego poszczególnych komponentów.
Bezpieczeństwo Zintegrowanych Systemów Produkcyjnych: Specyfikacja granic systemu
Określenie granic i funkcjonalności systemu produkcyjnego jest kluczowe dla właściwej oceny ryzyka i zapewnienia bezpieczeństwa. Granice systemu obejmują fizyczne i operacyjne ograniczenia, a także interfejsy między maszynami. Specyfikacja ta pozwala na dokładne zrozumienie, jakie elementy systemu muszą być uwzględnione w procesie oceny ryzyka. Dokumentacja funkcjonalna powinna zawierać szczegółowe opisy wszystkich maszyn i urządzeń wchodzących w skład systemu, ich interfejsów, a także procedur operacyjnych i konserwacyjnych. Takie podejście zapewnia, że wszystkie aspekty bezpieczeństwa są uwzględnione już na etapie projektowania systemu.
Ocena ryzyka musi obejmować wszystkie maszyny i urządzenia, które są częścią zintegrowanego systemu produkcyjnego, uwzględniając interakcje między nimi.
Zidentyfikowanie i oznaczenie stref zadaniowych
Wyznaczenie stref zadaniowych, w których operatorzy mogą bezpiecznie wykonywać swoje zadania, jest kluczowym elementem normy. Strefy te muszą być jasno oznaczone i wyposażone w odpowiednie środki ochronne, takie jak osłony maszyn, systemy detekcji obecności, blokady itp. Wyznaczenie stref zadaniowych pozwala na efektywne zarządzanie ryzykiem, umożliwiając operatorom bezpieczne wykonywanie zadań bez narażania się na niebezpieczeństwa związane z działaniem maszyn.
Różne tryby operacyjne
Norma wymaga zapewnienia różnych trybów operacyjnych, takich jak tryb automatyczny, ręczny czy serwisowy, które pozwalają na bezpieczne wykonywanie różnych zadań w systemie produkcyjnym. Każdy tryb operacyjny musi być odpowiednio zaprojektowany i wyposażony w środki ochronne, aby zapewnić bezpieczeństwo operatorów. Tryby operacyjne są szczególnie ważne w złożonych systemach produkcyjnych, gdzie konieczne jest przełączanie między różnymi trybami pracy w zależności od wykonywanych zadań.
Bezpieczeństwo Zintegrowanych Systemów Produkcyjnych: Kompleksowa dokumentacja
Dostarczenie szczegółowej dokumentacji technicznej jest niezbędne, aby użytkownicy systemu mogli bezpiecznie i efektywnie obsługiwać, konserwować i naprawiać zintegrowany system produkcyjny. Dokumentacja powinna zawierać informacje na temat wszystkich aspektów systemu, w tym procedur bezpieczeństwa, instrukcji obsługi, planów konserwacyjnych i opisów interfejsów między maszynami. Kompleksowa dokumentacja zapewnia, że wszystkie osoby zaangażowane w eksploatację systemu są świadome potencjalnych zagrożeń i wiedzą, jak bezpiecznie wykonywać swoje zadania. Jest to kluczowy element zarządzania ryzykiem i zapewnienia zgodności z normami bezpieczeństwa.
Bezpieczeństwo Zintegrowanych Systemów Produkcyjnych: Walidacja środków ochronnych
Przed uruchomieniem systemu, wszystkie środki ochronne muszą zostać zweryfikowane i potwierdzone jako skuteczne w redukcji ryzyka do akceptowalnego poziomu. Walidacja ta powinna obejmować testy funkcjonalne, przeglądy dokumentacji oraz audyty zgodności z normami zharmonizowanymi. Walidacja środków ochronnych jest kluczowa, ponieważ zapewnia, że wszystkie zabezpieczenia działają zgodnie z założeniami i skutecznie chronią operatorów przed zagrożeniami. Jest to niezbędne do uzyskania znaku CE i potwierdzenia zgodności z wymogami prawnymi.
Zabezpieczenia na poziomie systemu
Środki ochronne muszą być wdrażane nie tylko na poziomie poszczególnych maszyn, ale również na poziomie całego systemu produkcyjnego, aby zapewnić kompleksowe bezpieczeństwo maszyn. Zabezpieczenia muszą obejmować interfejsy między maszynami oraz zapewniać ochronę w przypadku awarii systemu. Zabezpieczenia na poziomie systemu obejmują takie elementy jak systemy zatrzymywania awaryjnego, detekcję obecności operatorów oraz systemy monitorowania stanu maszyn. Wszystkie te elementy muszą być zintegrowane w sposób zapewniający ich skuteczne działanie w całym systemie.
Dokumentacja techniczna powinna zawierać szczegółowe opisy procedur operacyjnych, konserwacyjnych oraz interfejsów między maszynami, aby zapewnić pełną zgodność z wymaganiami normy.”
Bezpieczeństwo Zintegrowanych Systemów Produkcyjnych: Muting i Blanking
Muting to tymczasowe automatyczne zawieszenie działania systemów bezpieczeństwa, takich jak czujniki obecności lub bariery świetlne, aby umożliwić przejazd materiałów przez strefę ochronną bez wywoływania alarmów lub zatrzymania maszyny. Jest to szczególnie użyteczne w zautomatyzowanych liniach produkcyjnych, gdzie regularne przerywanie pracy maszyn byłoby nieefektywne.
Kluczowe cechy mutingu:
- Tymczasowość: Muting jest zawsze czasowo ograniczony i ma na celu umożliwienie przejazdu materiałów przez strefę ochronną w określonych, kontrolowanych warunkach.
- Automatyzacja: Proces mutingu jest automatycznie kontrolowany przez system sterowania, który monitoruje warunki, takie jak prędkość ruchu i obecność obiektów, aby zapewnić, że muting jest stosowany tylko wtedy, gdy jest to bezpieczne.
- Bezpieczeństwo: Muting jest wdrażany w taki sposób, aby zminimalizować ryzyko dla operatorów. Na przykład, muting może być stosowany tylko wtedy, gdy operator nie jest obecny w strefie zagrożenia, a systemy detekcji obecności muszą być aktywne, aby zapobiec przypadkowemu wejściu operatora w strefę niebezpieczną.
Przykład zastosowania mutingu: Wyobraźmy sobie linię produkcyjną, gdzie taśma transportuje surowce przez różne etapy produkcji. Aby zapewnić ciągłość pracy, system może tymczasowo zawiesić działanie bariery świetlnej, gdy taśma transportuje materiał przez strefę ochronną. Po przejeździe materiału, bariera świetlna automatycznie wraca do trybu aktywnego, chroniąc operatorów przed wejściem w strefę niebezpieczną.
Blanking to wyłączanie części systemu detekcji obecności (np. czujników lub kurtyn świetlnych) w określonych obszarach, aby umożliwić normalne działanie maszyny bez przerw. Blanking jest szczególnie użyteczne w sytuacjach, gdy niektóre elementy maszyny lub transportowanego materiału mogą przechodzić przez strefę detekcji, ale nie stanowią zagrożenia dla operatorów.
Kluczowe cechy blankingu:
- Selektywność: Blanking polega na wyłączaniu tylko określonych czujników lub ich części, co pozwala na zachowanie funkcji ochronnych w innych obszarach.
- Kontrola: Proces blankingu jest ściśle kontrolowany i monitorowany przez system sterowania, który zapewnia, że wyłączone obszary nie stanowią zagrożenia.
- Adaptacyjność: Blanking może być dostosowywany do różnych sytuacji produkcyjnych, co pozwala na elastyczne zarządzanie bezpieczeństwem.
- Kluczowe cechy blankingu:
- Selektywność: Blanking polega na wyłączaniu tylko określonych czujników lub ich części, co pozwala na zachowanie funkcji ochronnych w innych obszarach.
- Kontrola: Proces blankingu jest ściśle kontrolowany i monitorowany przez system sterowania, który zapewnia, że wyłączone obszary nie stanowią zagrożenia.
- Adaptacyjność: Blanking może być dostosowywany do różnych sytuacji produkcyjnych, co pozwala na elastyczne zarządzanie bezpieczeństwem w zmieniających się warunkach pracy. W przypadku automatyki przemysłowej, adaptacyjność ta jest kluczowa, ponieważ umożliwia dynamiczne dostosowywanie systemów ochronnych do zmieniających się scenariuszy produkcyjnych.
Funkcja | Muting | Blanking |
---|---|---|
Definicja | Tymczasowe zawieszenie działania systemów bezpieczeństwa | Wyłączanie części systemu detekcji obecności w określonych obszarach |
Przykład zastosowania | Przejazd materiałów przez strefę ochronną w zautomatyzowanej linii produkcyjnej | Normalne działanie maszyny bez przerw, gdy niektóre elementy mogą przechodzić przez strefę |
Kluczowe cechy | Tymczasowość, automatyzacja, minimalizowanie ryzyka dla operatorów | Selektywność, kontrola, adaptacyjność do różnych sytuacji produkcyjnych |
Norma PN-EN-ISO 11161 podkreśla kluczowe aspekty zapewnienia bezpieczeństwa w zintegrowanych systemach produkcyjnych. Holistyczne podejście do oceny ryzyka, specyfikacja granic systemu, wyznaczanie stref zadaniowych, różne tryby operacyjne, kompleksowa dokumentacja, walidacja środków ochronnych, zabezpieczenia na poziomie systemu, oraz zaawansowane mechanizmy takie jak muting i blanking, są fundamentalnymi elementami skutecznego zarządzania bezpieczeństwem.
Projektanci maszyn oraz integratorzy automatyki przemysłowej muszą uwzględniać te wytyczne, aby zapewnić bezpieczne i efektywne działanie złożonych systemów produkcyjnych, zgodnie z najwyższymi standardami bezpieczeństwa i wymogami prawnymi. Stosowanie się do wymagań normy PN-EN-ISO 11161 nie tylko zwiększa bezpieczeństwo, ale także optymalizuje procesy produkcyjne, minimalizując ryzyko przestojów i awarii, co przekłada się na wyższą jakość produkcji i zadowolenie klientów.
W kontekście Dyrektywy Maszynowej 2006/42/WE oraz Rozporządzenia w sprawie maszyn 2023/1230, wdrażanie normy PN-EN-ISO 11161 stanowi istotny element zapewnienia zgodności z przepisami oraz uzyskania certyfikacji CE maszyn. Dzięki temu, systemy produkcyjne mogą być bezpiecznie użytkowane na rynku europejskim, spełniając wszystkie wymagania dotyczące bezpieczeństwa i zdrowia.
Automatyka przemysłowa to kluczowy element współczesnych linii produkcyjnych, który umożliwia zwiększenie efektywności i bezpieczeństwa operacji. Zespoły maszyn, zintegrowane za pomocą zaawansowanych systemów sterowania, takich jak SCADA i programowanie PLC, pozwalają na precyzyjne monitorowanie i kontrolowanie procesów produkcyjnych.
Integracja automatyzacji procesów produkcyjnych i zaawansowanych technologii, takich jak roboty przemysłowe oraz systemy SCADA i PLC, wymaga starannego zarządzania projektem oraz regularnych audytów bezpieczeństwa. Outsourcing inżynierów oraz współpraca z doświadczonym biurem konstrukcyjnym mogą znacznie zwiększyć efektywność i bezpieczeństwo projektów automatyzacji produkcji.
Ostatecznie, zastosowanie odpowiednich środków ochronnych oraz systematyczne monitorowanie i kontrolowanie stanu systemów produkcyjnych, zgodnie z wytycznymi normy PN-EN-ISO 11161, przyczynia się do tworzenia bezpiecznych i niezawodnych linii produkcyjnych, które spełniają najwyższe standardy jakości i bezpieczeństwa.
FAQ: Bezpieczeństwo Zintegrowanych Systemów Produkcyjnych
Odpowiedź: Norma PN-EN-ISO 11161 dotyczy bezpieczeństwa w zintegrowanych systemach produkcyjnych, składających się z wielu współpracujących maszyn. Ma na celu zapewnienie, że systemy te są projektowane i eksploatowane w sposób bezpieczny zarówno dla operatorów, jak i otoczenia.
Odpowiedź: Holistyczne podejście oznacza traktowanie zintegrowanego systemu produkcyjnego jako całości, a nie zbioru pojedynczych elementów. Ocena ryzyka musi uwzględniać interakcje między poszczególnymi maszynami, co zapewnia kompleksową ochronę i minimalizuje ryzyko związane z nieprzewidzianymi interakcjami.
Odpowiedź: Specyfikacja granic systemu produkcyjnego obejmuje fizyczne i operacyjne ograniczenia oraz interfejsy między maszynami. Jest kluczowa dla właściwej oceny ryzyka i zapewnienia bezpieczeństwa, umożliwiając dokładne zrozumienie, jakie elementy systemu muszą być uwzględnione.
Odpowiedź: Strefy zadaniowe muszą być jasno oznaczone i wyposażone w odpowiednie środki ochronne, takie jak osłony maszyn, systemy detekcji obecności i blokady. Pozwala to na efektywne zarządzanie ryzykiem i bezpieczne wykonywanie zadań przez operatorów.
Odpowiedź: Norma wymaga różnych trybów operacyjnych, takich jak tryb automatyczny, ręczny i serwisowy, aby bezpiecznie wykonywać różne zadania w systemie produkcyjnym. Każdy tryb musi być zaprojektowany z odpowiednimi środkami ochronnymi, aby zapewnić bezpieczeństwo operatorów.
Odpowiedź: Dokumentacja techniczna jest niezbędna do bezpiecznej i efektywnej obsługi, konserwacji i naprawy zintegrowanego systemu produkcyjnego. Powinna zawierać informacje na temat procedur bezpieczeństwa, instrukcji obsługi, planów konserwacyjnych i opisów interfejsów między maszynami.
Odpowiedź: Walidacja środków ochronnych obejmuje testy funkcjonalne, przeglądy dokumentacji i audyty zgodności z normami, aby potwierdzić ich skuteczność w redukcji ryzyka do akceptowalnego poziomu. Jest to kluczowe do uzyskania znaku CE i potwierdzenia zgodności z wymogami prawnymi.
Odpowiedź: Zabezpieczenia muszą być wdrażane nie tylko na poziomie poszczególnych maszyn, ale również całego systemu produkcyjnego. Obejmuje to systemy zatrzymywania awaryjnego, detekcję obecności operatorów oraz systemy monitorowania stanu maszyn.
Odpowiedź: Muting to tymczasowe automatyczne zawieszenie działania systemów bezpieczeństwa, aby umożliwić przejazd materiałów przez strefę ochronną bez wywoływania alarmów. Kluczowe cechy to tymczasowość, automatyzacja i minimalizowanie ryzyka dla operatorów.
Odpowiedź: Blanking to wyłączanie części systemu detekcji obecności w określonych obszarach, aby umożliwić normalne działanie maszyny bez przerw. Kluczowe cechy to selektywność, kontrola i adaptacyjność do różnych sytuacji produkcyjnych.
analiza ryzyka automatyka przemysłowa automatyzacja procesów produkcyjnych automatyzacja produkcji bezpieczeństwo maszyn deklaracja zgodności WE dokumentacja techniczna dostosowanie maszyn do wymagań minimalnych dyrektywa ATEX dyrektywa EMC dyrektywa LVD dyrektywa maszynowa 2006/42/WE Instrukcja obsługi integrator automatyki przemysłowej KPI linie produkcyjne maszyna nieukończona normy zharmonizowane ocena ryzyka OEE oznakowanie CE Performence level poka-yoke pokrycie diagnostyczne projektowanie maszyn przemysł spożywczy roboty przemysłowe rozporządzenie w sprawie maszyn 2023/1230 sat SCADA smed stanowiska zrobotyzowane TPM zarządzanie zarządzanie projektami Znak CE