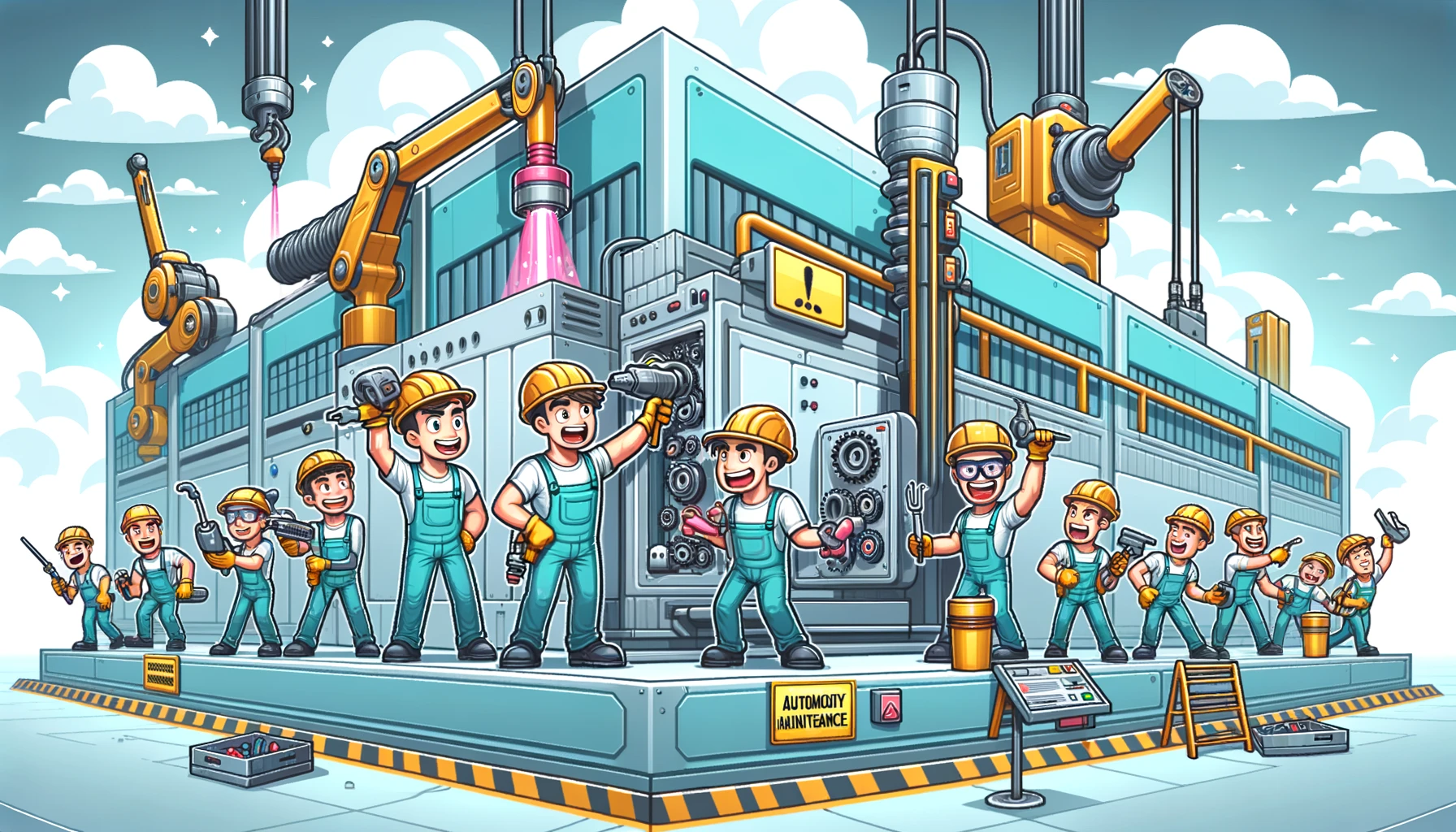
Total Productive Maintenance (TPM) to kompleksowe podejście do utrzymania ruchu, które łączy konserwację maszyn z innymi działaniami mającymi na celu maksymalizację wydajności i minimalizację awarii. W automatyce przemysłowej, Kompleksowe Utrzymanie Ruchu odgrywa kluczową rolę w zapewnieniu ciągłości procesów produkcyjnych, co jest niezwykle istotne w kontekście Przemysłu 4.0. W niniejszym artykule omówimy, czym jest TPM, jakie są jego kluczowe elementy oraz jak wpływa na projektowanie maszyn, automatyzację procesów produkcyjnych i zarządzanie projektami.
Spis Treści
Co to jest TPM?
TPM, czyli Total Productive Maintenance, to koncepcja zarządzania mająca na celu zwiększenie produktywności poprzez systematyczne podejście do utrzymania ruchu. Wprowadzona w Japonii w latach 70. XX wieku przez firmę Nippondenso (obecnie Denso), TPM łączy elementy prewencyjnego i predykcyjnego utrzymania ruchu z zaangażowaniem wszystkich pracowników w procesy konserwacji.
Total Productive Maintenance opiera się na idei, że odpowiednie zarządzanie utrzymaniem ruchu może przyczynić się do znacznego zwiększenia wydajności produkcji, redukcji kosztów operacyjnych oraz poprawy jakości produktów. Jest to szczególnie istotne w kontekście Automatyki przemysłowej i Przemysłu 4.0, gdzie niezawodność i efektywność maszyn odgrywają kluczową rolę.
Kluczowe Elementy Total Productive Maintenance
TPM składa się z ośmiu głównych filarów, które wspólnie tworzą kompleksowe podejście do utrzymania ruchu:
- Autonomiczne Utrzymanie Ruchu: Zaangażowanie operatorów maszyn w codzienne utrzymanie i konserwację sprzętu. Operatorzy są szkoleni w zakresie podstawowych zadań konserwacyjnych, co pozwala na szybkie wykrywanie i usuwanie drobnych usterek.
- Planowane Utrzymanie Ruchu: Regularne planowanie i przeprowadzanie konserwacji maszyn w celu zapobiegania awariom. W ramach planowanego utrzymania uwzględnia się zarówno rutynowe przeglądy, jak i bardziej zaawansowane działania, takie jak wymiana kluczowych komponentów. Biuro konstrukcyjne odgrywa tutaj kluczową rolę w projektowaniu maszyn, które są łatwe w utrzymaniu i zgodne z najnowszymi standardami.
- Utrzymanie Jakości: Integracja działań związanych z jakością z procesami konserwacyjnymi. Poprawa jakości produkcji poprzez eliminację źródeł wadliwych produktów oraz usprawnienie procesów produkcyjnych.
- Szkolenia i Edukacja: Zapewnienie odpowiednich szkoleń dla wszystkich pracowników zaangażowanych w procesy TPM. Edukacja obejmuje zarówno operatorów maszyn, jak i personel techniczny oraz menedżerów.
- Bezpieczeństwo, Zdrowie i Środowisko: Działania mające na celu zapewnienie bezpieczeństwa pracy, ochrony zdrowia pracowników oraz minimalizację wpływu na środowisko. TPM w dużej mierze opiera się na zgodności z Dyrektywą Maszynową 2006/42/WE i uzyskiwaniu Znaku CE, które są kluczowe dla zapewnienia bezpieczeństwa użytkowania maszyn.
- TPM w Nowym Wyposażeniu: Integracja zasad Total Productive Maintenance na etapie projektowania i zakupu nowych maszyn i urządzeń. Biuro konstrukcyjne odgrywa tu znaczącą rolę, wprowadzając idee takie jak POKA-YOKE i SMED, oraz przeprowadzając analizy FMEA i zasady Design for Assembly. Dzięki temu nowe maszyny są bardziej niezawodne i łatwe w utrzymaniu.
- Utrzymanie w Biurze: Wprowadzenie praktyk Total Productive Maintenance do obszarów biurowych w celu zwiększenia efektywności pracy i eliminacji marnotrawstwa.
- Podnoszenie Efektywności: Ciągłe doskonalenie procesów i maszyn w celu zwiększenia efektywności i produktywności. Kompleksowe Utrzymanie Ruchu wspiera pomiary i monitorowanie za pomocą systemów SCADA, co pozwala na dokładną analizę i optymalizację procesów produkcyjnych.
Filary TPM | Opis |
---|---|
Autonomiczne Utrzymanie Ruchu | Operatorzy maszyn są zaangażowani w codzienne utrzymanie i konserwację sprzętu. |
Planowane Utrzymanie | Regularne planowanie przeglądów i konserwacji maszyn w celu zapobiegania awariom. |
Utrzymanie Jakości | Integracja działań związanych z jakością z procesami konserwacyjnymi. |
Szkolenia i Edukacja | Szkolenia dla wszystkich pracowników zaangażowanych w procesy konserwacyjne. |
Bezpieczeństwo, Zdrowie i Środowisko | Działania mające na celu zapewnienie bezpieczeństwa pracy, ochrony zdrowia i środowiska. |
TPM w Nowym Wyposażeniu | Integracja zasad TPM na etapie projektowania i zakupu nowych maszyn i urządzeń. |
Utrzymanie w Biurze | Wprowadzenie praktyk TPM do obszarów biurowych. |
Podnoszenie Efektywności | Ciągłe doskonalenie procesów i maszyn w celu zwiększenia efektywności. |
5S i TPM: Jak Współdziałają dla Zwiększenia Efektywności Produkcji
5S to system organizacji miejsca pracy, który pochodzi z Japonii i jest integralną częścią filozofii lean manufacturing. Składa się z pięciu kroków: Sortowanie (Seiri), Systematyzowanie (Seiton), Sprzątanie (Seiso), Standaryzacja (Seiketsu) oraz Samodyscyplina (Shitsuke). Każdy z tych kroków ma na celu stworzenie czystego, uporządkowanego i wydajnego środowiska pracy.
Total Productive Maintenance (TPM) i 5S współdziałają w doskonały sposób, aby zwiększyć efektywność produkcji i utrzymanie maszyn. Oto jak te dwie metody wzajemnie się uzupełniają:
- Sortowanie (Seiri): Eliminacja zbędnych przedmiotów z miejsca pracy. W TPM sortowanie pomaga w usunięciu niepotrzebnych narzędzi i części, co zmniejsza ryzyko awarii maszyn spowodowanych przez nieodpowiednie elementy.
- Systematyzowanie (Seiton): Organizacja i oznakowanie niezbędnych przedmiotów. TPM korzysta z tego kroku, aby wszystkie narzędzia i części były łatwo dostępne i zorganizowane, co przyspiesza konserwację i naprawy maszyn.
- Sprzątanie (Seiso): Regularne czyszczenie miejsca pracy i maszyn. TPM podkreśla znaczenie czystości dla zapobiegania awariom. Czyste maszyny są mniej podatne na uszkodzenia, a ewentualne problemy są szybciej zauważane.
- Standaryzacja (Seiketsu): Utrzymywanie wysokich standardów organizacji i czystości. TPM korzysta z ustalonych procedur konserwacyjnych i standardów operacyjnych, które są wspierane przez standaryzację 5S.
- Samodyscyplina (Shitsuke): Kultywowanie nawyków i samodyscypliny wśród pracowników. TPM polega na zaangażowaniu wszystkich pracowników w procesy konserwacyjne, a 5S pomaga w utrzymaniu dyscypliny i systematyczności w działaniach konserwacyjnych.
Integracja 5S z TPM prowadzi do stworzenia bezpiecznego, wydajnego i dobrze zorganizowanego środowiska pracy. Poprzez wspólne stosowanie tych metod, firmy mogą znacząco poprawić wydajność produkcji, zmniejszyć liczbę awarii maszyn i zwiększyć zaangażowanie pracowników w utrzymanie wysokich standardów operacyjnych.
TPM a Projektowanie Maszyn
Projektowanie maszyn zgodnych z zasadami TPM jest kluczowe dla zapewnienia ich niezawodności i długowieczności. Uwzględniając Kompleksowe Utrzymanie Ruchu już na etapie projektowania, można osiągnąć znaczące usprawnienia w obszarach takich jak POKA-YOKE, SMED oraz przewidywanie utrzymanie ruchu.
- POKA-YOKE: Techniki zapobiegania błędom są integralną częścią TPM. Projektując maszyny z wykorzystaniem POKA-YOKE, inżynierowie mogą minimalizować ryzyko popełnienia błędów przez operatorów, co prowadzi do zwiększenia niezawodności i bezpieczeństwa.
- SMED (Single Minute Exchange of Die): Optymalizacja procesów zmiany narzędzi i formatów produkcyjnych. Projektowanie maszyn z myślą o SMED pozwala na skrócenie czasu przezbrojenia, co zwiększa elastyczność i efektywność produkcji.
- Przewidywanie utrzymania ruchu: Wykorzystanie zaawansowanych technologii do monitorowania stanu maszyn i przewidywania potencjalnych awarii. Dzięki integracji TPM z systemami SCADA i PLC, możliwe jest wczesne wykrywanie problemów i przeprowadzanie interwencji przed wystąpieniem awarii.
TPM ma również znaczący wpływ na spełnianie wymogów bezpieczeństwa maszyn, takich jak Dyrektywa Maszynowa 2006/42/WE i uzyskiwanie Znaku CE. Projektowanie maszyn zgodnych z Total Productive Maintenance pozwala na zapewnienie zgodności z normami bezpieczeństwa (normami zharmonizowanymi), co jest kluczowe dla uzyskania odpowiednich certyfikatów i dopuszczenia maszyn do użytku na rynkach międzynarodowych.
Wpływ Kompleksowe Utrzymanie Ruchu na GMP (Good Manufacturing Practices) i zgodność z normami FDA (Food and Drug Administration) jest również istotny. Projektowanie maszyn zgodnych z TPM zapewnia spełnienie rygorystycznych wymogów dotyczących jakości i bezpieczeństwa w przemyśle farmaceutycznym i spożywczym.
Total Productive Maintenance a Bezpieczeństwo Maszyn
Bezpieczeństwo maszyn jest kluczowym elementem w kontekście TPM. Zgodność z normami zharmonizowanymi oraz spełnianie wymogów Dyrektywy Maszynowej 2006/42/WE przyczynia się do zwiększenia wydajności i niezawodności produkcji.
- Normy Zharmonizowane: TPM promuje zgodność z normami zharmonizowanymi, które zapewniają najwyższe standardy bezpieczeństwa i niezawodności. Przestrzeganie tych norm minimalizuje ryzyko wypadków i awarii, co z kolei prowadzi do zwiększenia wydajności.
- Rola Biura Konstrukcyjnego: Biura konstrukcyjne odgrywają kluczową rolę w projektowaniu maszyn zgodnych z TPM. Inżynierowie projektujący maszyny uwzględniają zasady Total Productive Maintenance, co pozwala na tworzenie bezpiecznych, wydajnych i łatwych w konserwacji urządzeń.
- Bezpieczeństwo a Wydajność: Zwiększenie bezpieczeństwa maszyn poprzez zgodność z normami i Total Productive Maintenance wpływa pozytywnie na wydajność. Bezpieczne maszyny wymagają mniej przestojów związanych z naprawami i konserwacją, co przekłada się na ciągłość produkcji.
TPM w Automatyzacji Procesów Produkcyjnych
TPM odgrywa kluczową rolę w automatyzacji procesów produkcyjnych, wspierając integrację systemów SCADA oraz PLC.
- Automatyzacja Produkcji: Total Productive Maintenance wspiera automatyzację produkcji poprzez zapewnienie niezawodności i ciągłości pracy maszyn. Systemy SCADA i PLC umożliwiają monitorowanie stanu maszyn i szybką reakcję na ewentualne problemy.
- Maszyny Specjalne: Projektowanie maszyn specjalnych zgodnych z TPM pozwala na dostosowanie ich do specyficznych wymagań produkcyjnych. Maszyny te charakteryzują się wysoką niezawodnością i łatwością konserwacji, co jest kluczowe dla utrzymania ciągłości produkcji. Biuro konstrukcyjne odgrywa tu kluczową rolę, zbierając feedback od zespołu produkcyjnego i dostosowując projekt do specyficznych potrzeb klienta.
- Programowanie PLC: Wdrażanie Kompleksowe Utrzymanie Ruchu w programowaniu PLC pozwala na stworzenie bardziej efektywnych i niezawodnych systemów automatyki. Programy PLC są projektowane z myślą o minimalizacji ryzyka awarii i łatwości w konserwacji.
- Optymalizacja OEE: Total Productive Maintenance przyczynia się do optymalizacji wskaźnika OEE (Overall Equipment Effectiveness), który mierzy efektywność wykorzystania maszyn. Zastosowanie TPM pozwala na identyfikację i eliminację źródeł strat, co prowadzi do zwiększenia efektywności produkcji.
- Zarządzanie KPI: TPM wspiera zarządzanie KPI (Key Performance Indicators) poprzez systematyczne monitorowanie i analizę kluczowych wskaźników wydajności. Dzięki temu możliwe jest szybkie reagowanie na wszelkie odchylenia od normy i podejmowanie działań korygujących.
SCADA a Total Productive Maintenance: Jak Systemy Monitoringu Wspierają zarządzanie produkcją
W kontekście nowoczesnej automatyzacji produkcji, połączenie systemów SCADA (Supervisory Control and Data Acquisition) z filozofią Total Productive Maintenance tworzy potężne narzędzie do zarządzania i optymalizacji procesów przemysłowych. SCADA jest zaawansowanym systemem, który pozwala na monitorowanie i kontrolę procesów produkcyjnych w czasie rzeczywistym, podczas gdy Kompleksowe Utrzymanie Ruchu jest holistycznym podejściem do utrzymania ruchu i maksymalizacji efektywności maszyn. Razem te dwa elementy mogą znacząco poprawić wydajność, niezawodność i bezpieczeństwo w zakładach produkcyjnych.
Kluczowe Funkcje SCADA
- Monitorowanie w Czasie Rzeczywistym: SCADA umożliwia ciągłe monitorowanie stanu maszyn i procesów produkcyjnych. Dane są gromadzone w czasie rzeczywistym, co pozwala na szybką reakcję na wszelkie nieprawidłowości.
- Alarmy i Powiadomienia: Systemy SCADA mogą generować alarmy i powiadomienia w przypadku wykrycia problemów, takich jak awarie maszyn, przekroczenia limitów bezpieczeństwa, czy inne nieprawidłowości. Operatorzy są natychmiast informowani o problemach, co pozwala na szybką interwencję.
- Zarządzanie Danymi: SCADA gromadzi dane z różnych źródeł i przechowuje je w centralnej bazie danych. Dane te mogą być analizowane w celu identyfikacji trendów, wykrywania problemów oraz optymalizacji procesów produkcyjnych.
- Sterowanie Procesami: SCADA umożliwia zdalne sterowanie urządzeniami i procesami produkcyjnymi. Operatorzy mogą wprowadzać zmiany w ustawieniach maszyn, zarządzać procesami produkcyjnymi oraz przeprowadzać konserwację z jednego centralnego punktu.
Total Productive Maintenance w Zarządzaniu Projektami i Outsourcingu Inżynierów
Implementacja TPM w zarządzaniu projektami inżynieryjnymi oraz korzyści z Outsourcingu inżynierów.
- Zarządzanie Projektami: Kompleksowe Zarządzanie Produkcją wspiera zarządzanie projektami poprzez systematyczne podejście do planowania zakupów maszyn. Integracja TPM w projekty inżynieryjne pozwala na bardziej efektywne planowanie i realizację projektów.
- Outsourcing Inżynierów: Korzystanie z usług zewnętrznych biur konstrukcyjnych i inżynierów może przynieść wiele korzyści, takich jak dostęp do specjalistycznej wiedzy i doświadczenia. Outsourcing inżynierów wspiera wdrażanie TPM poprzez zapewnienie odpowiednich zasobów i ekspertyz.
Przyszłość TPM w Przemyśle 4.0
Jak TPM będzie się rozwijać w kontekście Przemysłu 4.0.
- Innowacje i Technologie: TPM będzie nadal ewoluować wraz z rozwojem nowych technologii i innowacji w Przemyśle 4.0. Wykorzystanie zaawansowanych systemów monitoringu i analizy danych pozwoli na jeszcze bardziej precyzyjne przewidywanie awarii i optymalizację procesów produkcyjnych.
- Integracja z IoT: Internet Rzeczy (IoT) odegra kluczową rolę w przyszłości TPM. Dzięki integracji z IoT możliwe będzie jeszcze bardziej efektywne monitorowanie i zarządzanie maszynami w czasie rzeczywistym.
TPM jest kluczowym elementem w automatyzacji produkcji, zapewniając niezawodność i wydajność maszyn. Implementacja Kompleksowe Utrzymanie Ruchu na różnych etapach projektowania, produkcji i utrzymania ruchu przynosi liczne korzyści, takie jak zwiększenie bezpieczeństwa, optymalizacja procesów i zgodność z normami. W kontekście Przemysłu 4.0, Kompleksowe Zarządzanie Produkcją będzie nadal ewoluować, wspierając rozwój nowych technologii i innowacji.
FAQ: Total Productive Maintenance (TPM)
Total Productive Maintenance (TPM) to holistyczne podejście do utrzymania ruchu, które ma na celu maksymalizację efektywności maszyn i minimalizację awarii poprzez zaangażowanie wszystkich pracowników w procesy konserwacyjne. TPM obejmuje osiem filarów, takich jak autonomiczne utrzymanie ruchu, planowane utrzymanie, utrzymanie jakości i inne.
TPM składa się z ośmiu głównych filarów: autonomiczne utrzymanie ruchu, planowane utrzymanie, utrzymanie jakości, szkolenia i edukacja, bezpieczeństwo, zdrowie i środowisko, TPM w nowym wyposażeniu, utrzymanie w biurze oraz podnoszenie efektywności. Każdy z tych filarów ma na celu zwiększenie wydajności i niezawodności maszyn.
Korzyści z implementacji TPM obejmują zwiększenie niezawodności maszyn, poprawę jakości produktów, zmniejszenie kosztów utrzymania ruchu, zwiększenie bezpieczeństwa pracy oraz wzrost efektywności produkcji. TPM pomaga również w zaangażowaniu pracowników w procesy konserwacyjne, co prowadzi do lepszego zarządzania zasobami.
TPM kładzie duży nacisk na bezpieczeństwo maszyn poprzez wprowadzenie standardów i procedur zgodnych z normami, takimi jak Dyrektywa Maszynowa 2006/42/WE i uzyskiwanie znaku CE. Zgodność z tymi normami minimalizuje ryzyko wypadków i awarii, co zwiększa bezpieczeństwo pracy i niezawodność maszyn.
Planowane utrzymanie ruchu w TPM polega na regularnym planowaniu i przeprowadzaniu konserwacji maszyn w celu zapobiegania awariom. Total Productive Maintenance wykorzystuje analizę danych historycznych i monitorowanie stanu maszyn, aby przewidywać, kiedy maszyna będzie wymagała konserwacji. Biura konstrukcyjne odgrywają kluczową rolę w projektowaniu maszyn łatwych w utrzymaniu.
TPM w nowym wyposażeniu polega na integracji zasad TPM na etapie projektowania i zakupu nowych maszyn. Biura konstrukcyjne wprowadzają idee takie jak POKA-YOKE, SMED oraz przeprowadzają analizy FMEA i zasady Design for Assembly, co sprawia, że nowe maszyny są bardziej niezawodne i łatwe w utrzymaniu.
Techniki POKA-YOKE stosowane w TPM obejmują mechanizmy blokujące nieprawidłowe operacje, sensory wykrywające niewłaściwe ustawienia oraz automatyczne systemy korekcji. Te techniki minimalizują ryzyko popełnienia błędów przez operatorów, co prowadzi do zwiększenia niezawodności i bezpieczeństwa maszyn.
Total Productive Maintenance kładzie duży nacisk na szkolenia i edukację pracowników, aby zapewnić, że wszyscy zaangażowani w procesy konserwacyjne mają odpowiednie umiejętności i wiedzę. Szkolenia obejmują zarówno operatorów maszyn, jak i personel techniczny oraz menedżerów, co pozwala na lepsze zarządzanie utrzymaniem ruchu i zwiększa efektywność produkcji.
TPM wpływa na jakość produktów poprzez integrację działań związanych z jakością z procesami konserwacyjnymi. Utrzymanie jakości obejmuje eliminację źródeł wadliwych produktów oraz usprawnienie procesów produkcyjnych, co prowadzi do produkcji wyrobów o wyższej jakości i zmniejszenia liczby wadliwych produktów.
10. Jakie są korzyści z integracji systemów SCADA z TPM?
Integracja systemów SCADA z Total Productive Maintenance przynosi wiele korzyści, takich jak zwiększona niezawodność maszyn, zwiększona efektywność produkcji, poprawa jakości produktów, zwiększone bezpieczeństwo pracy oraz optymalizacja kosztów utrzymania ruchu. SCADA umożliwia monitorowanie i analizę danych w czasie rzeczywistym, co wspiera podejmowanie lepszych decyzji dotyczących utrzymania ruchu.
analiza ryzyka automatyka przemysłowa automatyzacja procesów produkcyjnych automatyzacja produkcji bezpieczeństwo maszyn deklaracja zgodności WE dokumentacja techniczna dostosowanie maszyn do wymagań minimalnych dyrektywa ATEX dyrektywa EMC dyrektywa LVD dyrektywa maszynowa 2006/42/WE GPSD GPSR hazop Instrukcja obsługi integrator automatyki przemysłowej inżynieria procesowa KPI linie produkcyjne maszyna nieukończona mes normy zharmonizowane ocena ryzyka OEE oznakowanie CE Performence level poka-yoke pokrycie diagnostyczne projektowanie maszyn przemysł spożywczy roboty przemysłowe rozporządzenie w sprawie maszyn 2023/1230 sat SCADA SIL smed stanowiska zrobotyzowane TPM zarządzanie zarządzanie projektami Znak CE
Zobacz także:
Napisz do nas!
Chętnie odpowiemy na Twoje pytania!